Belt-driven pumps, conveyors and fans keep your plant in motion. Whether you are moving, processing or storing your product, there are probably some very important belt-driven assets at your plant that you can’t afford to lose. Their failure could lead to production line shutdowns, product contamination or even pose safety risk to your staff. Read on to find out how you can safely monitor such assets in order to run your facility with the confidence that everything is operating as it should.
The challenge
Chemical plants often contain ATEX zones or harsh environments where your workers won’t go unless absolutely necessary. It is in these zones that most of the time the most critical parts of your production process takes place. Closely monitoring the condition of assets located in these zones is both very challenging and very important–but it mustn’t come at the expense of your employees’ wellbeing.
The plant’s financial performance is at stake too: malfunctioning fans can lead to the accumulation of unwanted gasses; broken pumps to the contamination of sensitive solutions; a single faulty conveyor can interrupt your entire production line. This can result in hefty fines, unusable product batches or simply in the waste of the plant’s precious running time.
The solution
Samotics has developed a solution that allows for remote monitoring of critical assets. The SAM4 Health system uses a suite of techniques to analyze a motor’s electrical signature, extracted from the current and voltage signals being fed to the motor. This means its sensors are installed inside the motor control cabinet (MCC) by design, which allows for reliable monitoring of your pumps, fans and conveyors at a distance.
In the chemical industry, downtime and its associated impacts can come with significant financial and environmental costs, not to mention the safety risks that can result from a faulty asset. The following section will outline three case studies of how SAM4 HEALTH helped detect faults at an early stage. These detections ensured uptime and avoided potential damages of hundreds of thousands of euros.
1. Early warning of belt degradation on a circulation pump
SAM4 Health is installed on several assets at a chlor-alkali plant. The circulation of highly concentrated salt water is essential for the normal operation of the plant—several circulation pumps ensure that this demand is consistently met. In this specific case, the electrical data collected from one of these pumps showed a sudden increase in spectral energy around the belt frequency. The SAM4 Health system provided the customer a clear advice via a notification, recommending the maintenance team to inspect the belt driving this pump during the next planned maintenance stop.
And that is exactly what they did. Without any production losses, at a time that was convenient for the customer, they were able to inspect the pump that displayed anomalous behavior and confirm the detection: the belt needed to be replaced. Performing this intervention allowed normal plant operations to proceed as planned. Following the maintenance actions, the SAM4 dashboard confirmed that all critical assets were now performing as they should.

2. Early warning of bearing and pulley degradation on a winder exhaust fan
At a Kevlar production facility, SAM4 Health is monitoring several critical assets involved in the manufacturing process. One of them, a belt-driven exhaust fan, ensures that the ideal atmospheric conditions are maintained, venting out harmful particulates in the air which could affect the quality of the final product. Unbeknownst to the plant manager, some of the components of this fan–one of the bearings and the pulley–were beginning to deteriorate. To make matters worse, the redundant fan supposed to kick in in case the primary asset fails, was out of operation.
Only three weeks a er the initial installation, SAM4 Health was able to detect an unhealthy pa ern in the motor’s electrical signature: an increase in spectral energy at a frequency of about 7 Hz. The customer was notified immediately: the system sent out an alert, recommending an inspection of the full drivetrain. A er receiving this notification, the customer’s maintenance team promptly identified and replaced the faulty components. Following this intervention, the SAM4 Health data clearly showed that the electrical signatures went back to their healthy patterns, thus confirming that the intervention had been successful.
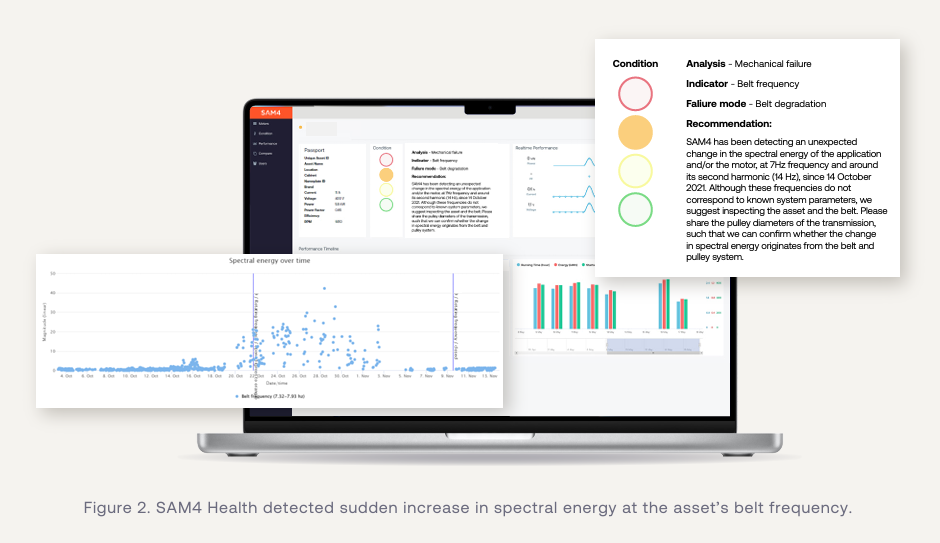
By flagging this issue, SAM4 Health was able to prevent unplanned downtime at this customer’s facility, and more importantly, no product batches were contaminated or damaged in any way.
3. Early warning of belt degradation on a salt conveyor
What happens when the conveyor that moves your final product to its pre-shipping storage unit fails? The entire production line is halted. That is what almost happened at a salt production plant where SAM4 Health is installed. Depending on how long it takes for the repairs to be carried out, this interruption in the process can cost a factory tens of thousands of euros. In this case, the plant manager could prevent the interruption and its consequences with the help of SAM4 Health data.
The system flagged some troubling behavior of the electric signal around 23 Hz, which was communicated to the customer via a notification. At the next turnaround the asset was inspected revealing a worn belt. If le unchecked this belt could eventually have snapped, interfering with the entire production process. But that wasn’t the case: the belt was replaced, production was resumed as planned, and not a single grain of salt was lost.

The major reason we chose SAM4 is because it’s easy to install in the motor control center, far away from our ATEX-zoned production systems. That greatly reduces the cost of equipment, installation and cabling, compared to traditional condition monitoring techniques that install on the physical equipment.
Joost Cuyckens, Asset Management Leader, Kuraray
The conclusion
Some of your most critical assets are susceptible to belt degradation issues, and many of them are hard to monitor. This is especially true for plants which contain dangerous zones such as ATEX zones, where the risk is not only financial: human lives are at stake. Samotics’ remote monitoring solution ensures that small faults do not create big headaches by preventing catastrophic accidents and providing actionable insights that help you run your chemical plant at an optimal configuration. This document has outlined a few examples, but this list is by no means exhaustive.