Electrical Signature Analysis
Unplanned downtime costs industries billions each year, disrupting operations and hitting profitability hard. Electrical Signature Analysis (ESA) offers a proactive approach to machine condition monitoring, helping organizations detect issues early, minimize unplanned downtime, and improve reliability.
This blog explores what ESA is, how it works, the faults it can detect, and how it compares to other condition monitoring techniques. We’ll also look at its benefits, real-world applications, and why it’s a valuable tool for modern maintenance strategies.
What is Electrical Signature Analysis (ESA)?
Electrical Signature Analysis (ESA) is a non-intrusive condition monitoring technique that uses current and voltage to detect subtle changes in a machine’s operation. These changes can indicate potential faults, giving you time to schedule maintenance before failure occurs.
ESA differs from other condition monitoring techniques, such as vibration analysis or temperature-based systems, which rely on sensors placed directly on the equipment. Instead, ESA monitors electrical data from a distance, analyzing how the operation of the connected motor affects its magnetic field, and subsequently the current and voltage. This makes it particularly useful for monitoring machines in hazardous or hard-to-reach environments.
The origins and evolution of ESA
Electrical Signature Analysis (ESA) can be traced back to 1985, when the Oak Ridge National Laboratory developed Motor Current Signature Analysis (MCSA) to non-intrusively monitor motor-operated valves in nuclear power plants. This innovation transformed fault detection in critical operations by enabling real-time motor data collection.
Building on this foundation, ESA evolved to include voltage and power monitoring, expanding its capabilities to pumps, compressors, and other rotating equipment by the 1990s. This non-intrusive approach became essential for minimising downtime and detecting issues like bearing wear and rotor imbalances.
In the 2010s, the integration of real-time data and advanced analytics propelled ESA into predictive maintenance, helping operators reduce costs and improve efficiency. Today, powered by IIoT and AI, ESA ensures reliability while driving energy efficiency and sustainability across industries.
How ESA works
The process of ESA involves two main stages: data capture and data analysis. Both are essential for identifying faults and enhancing the reliability of machinery.
Step 1: Data capture
The first step in ESA is to install permanent sensors in the motor control cabinet, where they can continuously capture high-frequency electrical data from the machine. ESA’s sensors are different from those used in other condition monitoring systems like vibration analysis, which require sensors to be placed on the machine itself. With ESA, the sensors monitor the machine’s current and voltage remotely, without the need for direct physical access.
This offers several advantages:
- Safety: Sensors are protected from harsh environments, such as high temperatures or hazardous areas.
- Ease of installation: Since the sensors are placed in the motor control cabinet, they are shielded from operational hazards like heat, vibration, or liquid exposure.
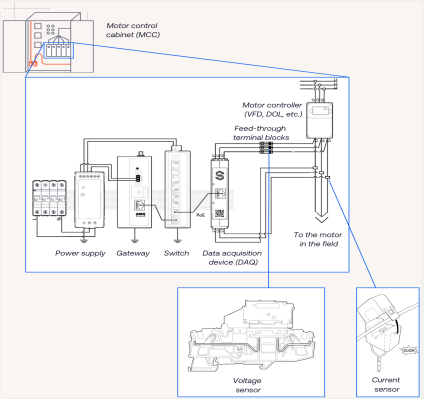
Step 2: Data analysis
Once the electrical data is captured, ESA uses a variety of algorithms to analyze it. The most fundamental algorithm in ESA is the Fast Fourier Transform (FFT), which converts time-domain data into the frequency domain. This analysis reveals the machine’s frequency signature, a detailed map of its operational state.
Beyond FFT, ESA uses other methods such as:
- Spectral analysis: Helps to map out the strength of different frequencies in the electrical signal.
- Power analysis: Identifies issues like voltage unbalance and harmonic distortion, which can affect machine performance.
- Lateral and torsional analysis: Provides insights into the machine’s rotational and back-and-forth movements, giving a complete picture of its mechanical health.
Through this continuous data analysis, ESA can identify changes in the machine’s electrical signature that indicate developing faults. ESA’s non-intrusive data collection and comprehensive analysis make it a versatile and reliable tool for condition monitoring.
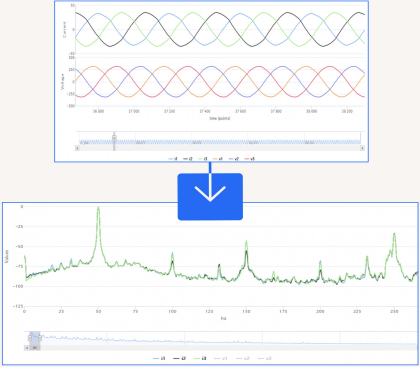
Types of faults detected by ESA
ESA is a highly effective method for uncovering faults in equipment by analyzing subtle changes in current and voltage. It excels at identifying both mechanical and electrical issues early, enabling targeted maintenance before problems escalate. By pinpointing these faults, ESA helps minimize unplanned downtime and extend equipment lifespan.
Mechanical fault detection with ESA
ESA is exceptional at identifying mechanical faults in machines. Mechanical issues like bearing wear, misaligned couplings, or pump cavitation cause subtle changes in the motor’s operation, which affect the magnetic field and, in turn, the machine’s electrical signature. ESA can detect these changes early by identifying frequency fingerprints specific to certain mechanical faults.
For instance, when a bearing begins to wear, ESA will detect an increase in energy at frequencies associated with the bearing’s physical characteristics. These include:
- Fundamental train (cage) frequency – reflects the movement of the cage guiding the rolling elements;
- Ball pass inner race frequency – indicates potential issues with the inner race of the bearing;
- Ball pass outer race frequency – used to detect defects in the outer race;
- Ball spin frequency – can identify defects on the rolling elements themselves.
By monitoring these frequencies, ESA can pinpoint the development of mechanical faults in the drive train, allowing for timely repairs.
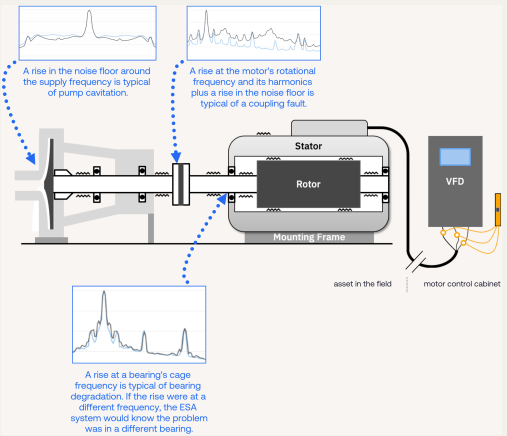
Electrical fault detection with ESA
ESA is particularly effective at detecting electrical faults, which account for around 30% of motor failures in industrial applications. Electrical problems can have a direct impact on the machine’s magnetic field, and by analyzing current and voltage, ESA provides early detection of these issues.
Some common electrical faults that ESA can identify include:
- Broken rotor bars: These cause imbalances in the motor’s magnetic field, and ESA detects the irregularities in the electrical signature.
- Stator faults: ESA can detect winding insulation issues or short circuits in the stator before they escalate.
- Bearing currents: In certain scenarios, stray currents in bearings can lead to overheating and premature wear. ESA can detect signs of these currents early, helping reduce the risk of further damage.
Since ESA measures the machine’s electrical signature directly, it can detect these faults earlier than other condition monitoring systems that focus on vibration or temperature data.

Benefits of ESA: real-time performance & energy monitoring
ESA is more than a fault detection system—it’s a tool designed to improve machine performance and energy efficiency. By providing real-time electrical data, it helps you keep your operations reliable and identify ways to reduce energy costs.
Real-time insights for everyday challenges
ESA provides insights into your machines’ performance, such as unusual motor vibrations that signal bearing wear or energy spikes pointing to inefficiencies. These insights help you plan maintenance, replace parts before breakdowns, and adjust settings for better efficiency. They also support decisions like upgrading equipment or prioritising repairs for critical machinery.
Practical ways ESA adds value:
- Pump efficiency monitoring
Tracks pump performance, addresses issues such as cavitation, and extends the life of key components such as bearings. - Power quality monitoring
Detects problems such as voltage imbalances or harmonic distortion early, preventing performance issues and unnecessary energy loss. - Energy consumption tracking
Analyzes long-term trends in energy use to uncover opportunities for efficiency improvements and cost savings.
A tool to simplify optimisation
With its real-time monitoring and actionable insights, ESA is a practical solution for maintaining reliability and improving efficiency. Whether it’s tackling energy use or enhancing machine performance, it helps you approach operations with confidence.
Key industries benefiting ESA
Electrical Signature Analysis has proven itself indispensable in industries where reliability and efficiency directly impact profitability and safety. By detecting faults early and offering actionable insights, ESA helps businesses avoid costly breakdowns and maintain operational excellence. Here are specific examples of how ESA delivers value across sectors:
1. Manufacturing
In high-speed production environments, even a minor fault can disrupt operations. ESA continuously monitors motors and conveyors to detect issues, such as rotor imbalances or bearing wear, commonly found in packaging lines or assembly systems. By addressing these problems early, manufacturers can prevent costly production delays and extend equipment lifespan.
2. Energy and Utilities
Power plants use ESA to keep generators, transformers, and power systems running at their best. For example, it can detect stator winding insulation faults early, preventing major failures and protecting the energy supply. It also helps maintain balanced voltage across systems, enhancing efficiency and ensuring reliable performance.
3. Oil and Gas
In remote or hazardous environments, such as offshore rigs, ESA is valuable for monitoring pumps and compressors. By detecting cavitation or stray bearing currents early, ESA reduces downtime and minimizes the risk of safety incidents. Its ability to operate in harsh conditions makes it a trusted solution for maintaining uptime in this sector.
4. Transportation
Rail networks and transit systems depend on ESA to keep electric motors in optimal condition. For example, it can detect overheating or misalignment in motors powering railcars, ensuring passenger safety and preventing costly service disruptions. ESA’s non-intrusive nature is especially valuable in these high-demand systems.
5. Water Treatment
In water and wastewater facilities, ESA monitors pumps and motors to ensure uninterrupted operation. It excels at detecting flow inefficiencies or cavitation that could compromise water processing. By keeping systems running efficiently, ESA supports consistent service delivery in critical public utilities.
6. Renewable Energy
ESA is a key enabler of reliability in renewable energy systems. For example, in wind turbines, ESA can detect gearbox wear or generator faults before they impact energy production. Its insights help operators reduce repair costs and optimize energy output, aligning with the sector’s sustainability goals.
7. Data Centers
With uptime being non-negotiable, data centers use ESA to monitor power distribution units, cooling systems, and backup generators. It identifies issues like voltage imbalances or overheating that could jeopardize operations. By ensuring equipment reliability, ESA supports the continuous functioning of these critical facilities.
Challenges in implementing ESA
Implementing ESA presents several challenges that organisations need to address to unlock its full potential.
Specialised knowledge is essential for deploying and interpreting ESA effectively. Without proper training, teams may struggle to use its advanced fault detection capabilities.
Upfront costs for sensors, hardware, and integration can also be a hurdle, especially for smaller businesses, though these investments often pay off through reduced downtime and maintenance savings.
Managing large volumes of high-frequency data requires efficient tools to avoid missing critical insights.
Integration with existing equipment is another challenge, particularly in facilities with older or varied machinery, which may require additional resources to ensure compatibility.
Resistance to adopting new technologies is also common, as teams may stick to familiar methods and underestimate ESA’s benefits in improving reliability and energy efficiency.
How to get started with ESA
Embarking on the journey with Electrical Signature Analysis doesn’t have to be daunting. By breaking it into clear, manageable steps, you can set up an effective system that fits your equipment and operational needs.
1. Define your monitoring goals
What do you want to achieve? Whether it’s detecting rotor bar issues in induction motors or monitoring commutator wear in DC motors, clear goals will guide your setup. Consider factors like the equipment’s environment and maintenance history to prioritise where ESA can deliver the most value.
2. Map out your implementation plan
Plan how ESA will fit into your existing operations. Decide on sensor placement, data collection, and analysis processes. For critical or high-voltage assets, include additional safety precautions and redundancies. A detailed plan ensures a smooth rollout and maximises results.
3. Choose the right ESA system supplier
Choosing the right ESA system supplier can make implementation far easier. A reliable provider will have the expertise to guide you through every step, from sensor installation to system integration. Look for a supplier with industry experience, strong support services, and scalable solutions that grow with your needs. With the right partner, you’ll experience a seamless setup with minimal disruption.
4. Ensure seamless integration
Your ESA system should fit effortlessly into your existing infrastructure. If you use IIoT platforms, integration may be straightforward. For older equipment, the right supplier can help bridge compatibility gaps, ensuring your system works smoothly.
5. Train your team
Equip your team with the knowledge they need to succeed. Offer tailored training—basic fault detection for simpler setups and advanced diagnostics for more complex systems. A confident team is essential for interpreting data and acting effectively.
ESA vs other condition monitoring techniques
ESA excels at detecting both electrical and mechanical faults, offering powerful insights not easily matched by other methods. One of its standout advantages is its ability to monitor hard-to-reach assets, such as submerged pumps, encased motors, or equipment located in hazardous or restricted areas. With sensors installed safely in the motor control cabinet, ESA eliminates the need for direct access to the equipment, making it a practical and efficient solution for challenging environments.
Below, we compare ESA with Vibration Analysis and Thermal Imaging—two other widely used techniques—to highlight the strengths and limitations of each. This comparison can help you identify which method best aligns with your operational needs.
Feature | Electrical Signature Analysis (ESA) | Vibration Analysis | Thermal Imaging (Infrared) |
Monitoring method | Non-intrusive, based on electrical data (current and voltage) | Intrusive, based on physical vibration data | Non-intrusive, based on surface temperature readings |
Data type analyzed | Current and voltage signals | Vibration signals | Infrared heat signatures |
Faults detected | Electrical (e.g., rotor bars) and mechanical (e.g., bearing wear) | Primarily mechanical (e.g., misalignments, bearing wear) | Overheating, insulation breakdowns, thermal imbalances |
Sensor placement | Sensors in motor control cabinet, no direct contact with equipment | Sensors placed directly on equipment | Line-of-sight required, no direct equipment contact |
Suitability for remote monitoring | Highly suitable, ideal for inaccessible or hazardous locations | Limited, requires sensor placement at the site | Limited, requires direct visual access to components |
Detection timing | Early detection, often before vibration or temperature anomalies occur | Intermediate, often after faults have developed | Intermediate, detects existing faults but not predictive |
Scalability | High, easily scalable across multiple assets | Moderate, requires sensors on each asset | Low, manual inspections limit scalability |
Integration with IIoT | Highly compatible, integrates with IIoT platforms for advanced analytics | Moderately compatible, requires additional setup for IIoT | Low compatibility, typically a standalone tool |
Cost of implementation | Moderate to high (upfront cost but long-term savings) | Moderate (sensor cost depends on the number of assets monitored) | Low to moderate (handheld cameras can be cost-effective) |
Why choose ESA over other condition monitoring techniques?
ESA offers a significant advantage for detecting electrical faults, such as broken rotor bars and stator problems, where it is more effective and economical than other techniques. While bearing faults may be more easily detected through vibration analysis, ESA can also detect them, making it a versatile solution.
Moreover, ESA can also identify faults like mechanical misalignment, air gap issues, supply irregularities, and insulation problems, making it a comprehensive tool for motor diagnostics. Its ease of implementation, even on hard-to-reach assets like submerged pumps or equipment in hazardous zones, adds to its practicality. Combined with its compatibility with IIoT systems and scalability, ESA is an excellent standalone or complementary condition monitoring method for broader fault detection and root cause analysis.
ESA case studies and real-world examples
From enhancing pump reliability in power plants to detecting transformer faults in wind power systems and diagnosing gearbox issues in industrial equipment, ESA has proven its value in diverse applications. These real-world examples show how ESA enables timely maintenance and optimizes equipment performance:
1. Improving pump reliability in a power plant
In a nuclear power facility, ESA was used to monitor two 350-horsepower motors driving vertical service water pumps. Traditional testing methods failed to detect underlying performance issues, but ESA quickly identified turbulence in the system caused by mechanical faults. Early detection allowed the plant to take timely corrective action, avoiding unplanned downtime and ensuring critical operations continued smoothly.
2. Identifying transformer issues in wind power
In another scenario, ESA was applied to a transformer in a wind power system to uncover performance anomalies. The analysis revealed significant electrical unbalance and loose connection signatures that weren’t visible through standard monitoring techniques. Addressing these faults not only resolved the immediate issue but also enhanced the long-term reliability of the transformer.
3. Pinpointing gearbox faults in industrial equipment
In an industrial application, ESA was used to analyze a motor and its attached gearbox. The data revealed an unusual signal indicating looseness outside the motor, which was traced to a faulty gearbox. This insight enabled maintenance teams to act before the issue escalated, preventing costly unplanned downtime and extending the life of the equipment.
Future trends in ESA technology
The future of Electrical Signature Analysis (ESA) is being shaped by a combination of technological advancements and the growing demand for reliability, efficiency, and sustainability in industrial operations. ESA is evolving from a traditional condition monitoring tool into a predictive solution that provides earlier and more precise fault detection.
Key innovations, such as AI and machine learning, are driving ESA’s evolution from a reactive tool to a predictive maintenance solution, delivering actionable insights that improve decision-making. Complementing this, the integration of ESA with Industrial Internet of Things (IIoT) platforms and cloud-based analytics enables scalable, real-time monitoring across multiple sites. This reduces reliance on on-site resources and supports faster, more effective responses to potential issues.
At the same time, sensor technology is becoming more robust and precise, ensuring reliable performance even in harsh or complex environments. Centralised data processing and advanced algorithms, such as Fast Fourier Transform (FFT), further enhance fault detection accuracy and streamline diagnostics. Combined with intuitive user interfaces, these advancements make ESA increasingly practical and accessible across industries.
By blending predictive analytics, seamless integration, and user-friendly design, ESA is not only keeping pace with technological advancements but also shaping the future of condition monitoring and machine protection.
Samotics’ ESA system (SAM4)
Samotics’ ESA system, SAM4, takes condition monitoring to the next level by pairing advanced machine learning with high-frequency electrical data collection. Installed directly in the motor control cabinet, it delivers insights that help you keep your assets running reliably, efficiently, and sustainably.
Monitor remotely, even in tough environments
With sensors safely installed in the motor control cabinet, SAM4 captures 24/7 data on current and voltage without the need to access the equipment itself. This makes it perfect for hard-to-reach or hazardous locations, like submerged pumps, motors encased in machinery, or ATEX zones. Better yet, installation is quick and straightforward—usually taking less than 30 minutes per machine.
Detect failures early and accurately
SAM4 excels at catching both electrical and mechanical issues before they cause downtime. From rotor bar damage to misaligned couplings, SAM4 pinpoints over 90% of faults—often up to five months in advance. By monitoring how mechanical problems affect electrical signals, SAM4 provides the insight you need to act early and avoid costly breakdowns.
Optimise performance and cut energy costs
SAM4 doesn’t just spot problems—it also helps you run your equipment better. Its advanced tools include:
- Pump monitoring to keep pumps at their most efficient operating point, cutting down on wear and tear.
- Energy monitoring to highlight inefficiencies and identify where redesign or replacement could save money and energy.
- Power quality monitoring to fix supply-side issues like voltage unbalance and harmonic distortion.
Conclusion
ESA is a powerful solution for improving operational reliability and efficiency across various industries. By offering early fault detection, improved energy efficiency, and real-time insights, ESA empowers organisations to optimise their maintenance strategies, reduce costs, and enhance reliability.
Whether it’s preventing unplanned downtime in manufacturing, safeguarding critical infrastructure in power generation, or maintaining uptime in challenging environments like oil rigs and water treatment facilities, ESA delivers measurable value. Its ability to integrate seamlessly with IIoT platforms and leverage AI-driven analytics positions it as a future-proof solution in a world increasingly focused on sustainability and efficiency.
For businesses looking to stay ahead of evolving demands and competitive pressures, ESA should be seen as a strategic investment in reliability, cost savings, and sustainable growth.
If you’re ready to discover how ESA can transform your operations, we’d be happy to tell you more about our ESA solution, SAM4.
FAQs about ESA
How does ESA improve energy efficiency?
By tracking energy consumption and identifying inefficiencies like harmonics or load imbalances, ESA highlights areas for improvement that can reduce energy costs.
How often should ESA data be analysed?
Analysis frequency depends on the criticality of the equipment, but real-time monitoring is preferred for high-value or critical assets.
Does ESA work with variable frequency drives (VFDs)?
Yes, ESA can monitor motors controlled by VFDs, but the analysis may require adjustments due to the electrical noise generated by the drives.
How quickly can I expect results from using ESA?
Benefits like fault detection and energy insights can often be realised immediately, with long-term savings increasing over time as trends and efficiencies are addressed.
Is ESA scalable for large facilities?
Yes, ESA systems can monitor multiple assets across a large facility, with centralised software to analyse and display performance data in real time.
Can ESA be used in remote monitoring setups?
Yes, many ESA solutions offer remote monitoring capabilities, enabling operators to track equipment performance and energy usage from anywhere.
What is required to integrate ESA into existing systems?
ESA systems typically require electrical panel access and may integrate with existing condition monitoring or asset management platforms through software or APIs.
What are the long-term monetary savings I can expect from ESA?
For example, a water pump running continuously at 100 kW with an electricity cost of €0.10 per kWh would use about €87,600 in energy each year. By using ESA to detect issues like cavitation early, energy efficiency can improve by roughly 10%, saving around €8,760 annually. Most industries see a return on investment in 1–3 years, making ESA a smart choice for cutting costs and improving operational efficiency.