Water utilities around the world are facing considerable challenges, such as aging infrastructure, extreme weather events and rapid population growth. All of these factors are significantly affecting performance of existing water systems, making issues like blockages, sewer overflows, leaks and asset failures more likely and more frequent. In response, many organizations are improving and optimizing the way they operate and maintain their critical equipment through a proactive maintenance approach. This smarter way of doing maintenance can help address equipment failure from age and damage while offering significant operational benefits. So what more can teams at water utilities achieve with a proactive approach?
What is proactive maintenance?
Most proactive maintenance strategies are a mix of preventive and condition-based maintenance (CBM) initiatives. Preventive maintenance uses regularly scheduled visits to ensure equipment is running well, rather than just sending teams in when something has already failed (reactive maintenance). CBM goes a step further and uses techniques that measure one or more physical parameters of equipment’s condition—current, voltage, lubricant, vibration, etc.—to identify changes in a machine’s behavior that signal a developing fault. By estimating the condition of assets, teams can schedule timely maintenance interventions and avoid unexpected failures.
With the rise of artificial intelligence (AI) and the industrial internet of things (IIoT), condition monitoring technologies can now continuously analyze vast amounts of incoming sensor data. This brings additional benefits to a condition-based maintenance approach that is powered by AI-based condition monitoring systems.
Real-time asset health status alerts allow repairs to be scheduled as needed, eliminating the high cost and safety risks of emergency callouts and repairs—and the even higher reputational and regulatory costs of a pollution incident or a water supply interruption. Companies can optimize their use of scarce maintenance resources without compromising reliability. There are cost savings to be found at every stage, from unexpected equipment issues to assets running in a non-optimal condition for an extended period of time.
Three ways to cut operational costs with a proactive maintenance approach
In this blog post, we’ll highlight three benefits of proactive maintenance that help lower operational costs and optimize maintenance resources. To do that, we’ll use real-world examples from wastewater companies who use our condition monitoring technology, SAM4 Health.
Benefit 1: Reduce the number of check-see visits
With water utilities’ pumping stations and treatment plants spread throughout the country—sometimes in extremely remote areas, check-see visits are time-consuming. They’re also rarely effective. A fault can develop the week or even the day after an inspection without there having been any warning sign during that previous visit. This time spent on regular inspections of remote stations would be a high operational cost in any climate, but it’s especially expensive in the face of skilled labor shortages.
For instance, one of our wastewater customers traditionally scheduled around 70,000 maintenance visits every year. As is often the case, they have many sewage pumping stations in remote areas. They checked these stations frequently to prevent the risk of a pollution event due to pump blockages. These many visits usually found the stations to be in a good working order. Implementing SAM4 Health gave the utility a reliable and continuous insight into the condition of assets at each pumping station. This, in turn, enabled them to reduce those non-value adding visits, prioritize their maintenance and optimize staff scheduling.
In one specific case, the water utility had a remote pumping station with two co-located pumps operating in an alternating duty-standby regime. One night, SAM4 Health detected signs of developing clogging in one of the pumps. Data analysis suggested a partial blockage that didn’t necessitate an emergency response, as the other pump was still capable of fulfilling the station’s duties. The situation was monitored and 48 hours later, an orange alert let the customer know that the incident was ongoing, but the situation could be resolved within a week.
A week or so later, SAM4 detected signs of a developing blockage on the second pump, prompting an urgent red alert. A maintenance team immediately went to the pumping station, lifted both pumps and discovered two partial blockages. They were cleared, and the pumps were quickly put back into operation.
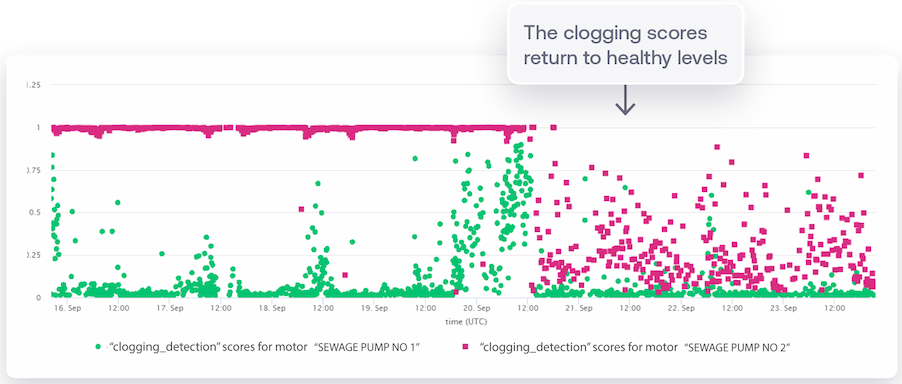
Accurate condition monitoring and insights into severity of the issue allowed the water company to optimize maintenance planning while preventing the risk of pump damage and a potential pollution event, which can incur a fine of up to €150,000 per incident.
Benefit 2: Reduce reactive maintenance works
From equipment rental to personnel overtime to supply costs, it is incredibly expensive to wait to do repairs until there’s a problem. At best, reactive repairs can mean expensive emergency mitigation. In the worst-case scenario, waiting until there is a problem like an asset failure can result in a pollution incident, which has high environmental and reputational costs alongside eye-watering fines. With condition-based maintenance, on the other hand, teams can plan repairs and replacements for any single asset in advance.
Consider the following case. SAM4 Health has been installed on a setup of four wastewater inlet screw pumps that lift and filter the flow coming into a large treatment plant. In one particular case, SAM4 Health detected an increase in spectral energy at two belt-related frequencies. SAM4 advised the customer that in addition to inspecting the belts, they should inspect the complete drivetrain to ensure that the belt issues have not caused stress in a different part of the system that might lead to a failure down the line.
The customer’s engineer determined that the belts were incorrectly tensioned and, when he inspected the complete drivetrain, he noticed there were some loose bolts as well as a bearing issue at the inlet of the gearbox. The customer created a planned work order to perform the required maintenance on the belts and gearbox. After maintenance was performed, SAM4 Health confirmed the screw pump had returned to healthy behavior.

The customer had not been aware of any issues with the Archimedes screws and noted that this early warning saved them €360,000 in emergency mitigation costs and €120,000 in post-failure repairs. They also valued the ability to plan the required maintenance at a convenient time, when the other inlet screws were able to handle all the incoming flow, avoiding a potential pollution risk.
Benefit 3: Lower repair and replacement costs
Early and accurate condition-based assessment means that companies can dramatically lower repair and replacement costs. Rather than replace parts according to a period of use, companies can wait until a replacement is needed based on the condition of an asset. More importantly, repairs can be planned in advance, avoiding unplanned downtime and minimizing rework and parts shortages.
As an example, another water customer installed Samotics’ SAM4 Health solution on four aeration rotors at a wastewater treatment plant. The system detected an increase in spectral energy at the rotational frequency of the motor, which is an indicator for mechanical unbalance. The customer also had a vibration condition monitoring system installed on the rotor, but that system had not yet sent an alert of an anomaly. Following the notification, the customer was able to schedule the maintenance so the site capacity wouldn’t be disrupted and replaced the gearbox that was the source of the detected unbalance. After this maintenance, SAM4 confirmed a return to healthy behavior.

Due to this timely alert, the customer was able to schedule and perform the required maintenance without disruption to site capacity, and at a time when repairs could be done quicker and cheaper. They estimated that SAM4’s notification prevented €54k in maintenance costs, €40k in emergency mitigation costs, and up to €400k in pollution event fines.
Reducing energy costs
It’s also worth noting the potential for energy optimization. Many water utilities are reducing energy as part of a net zero plan, but there are significant cost savings to be found in energy reduction as well. Real-time asset status alerts allow maintenance teams to address issues early on, which keeps pumps operating efficiently. Over time, this data can also offer significant insight into places across the system to reduce energy consumption and considerably raise reliability.