During dry periods, decreased water availability and increased demand strain an already delicate balance. As groundwater levels recess during drought season, shallower boreholes dry up, making it critical to keep every remaining borehole pump working effectively. By continuously monitoring these pumps’ health and performance in real time, water companies can proactively prevent borehole failures and avoid interruptions to supply. Thermal, oil and vibration analysis are excellent condition monitoring methods, but they require localized sensors, which cannot withstand the waterlogged conditions in which borehole pumps operate. Fortunately, there’s a less well-known technology called electrical signature analysis that makes reliable, remote monitoring of submerged pumps possible.
Climate change is a real and long-term threat to water security. Around the world, water companies are working hard to keep their harvesting, treatment and distribution systems resilient. New AI-based condition monitoring technology plays a crucial role in these efforts. For example, automated drones and “pipebots” can continuously patrol thousands of kilometers of piping to detect and localize cracks, weaknesses and existing leaks in a fraction of the time it would take human engineers.
But piping is just the tip of the iceberg. Wireless sensors and machine learning are replacing handheld instruments and human analysis to monitor every part of the water supply network. For some equipment, the move is straightforward — but borehole pumps present a unique condition monitoring challenge.
Solving the data capture problem for borehole pumps
To continuously measure vibrations, temperature or oil quality, sensors need to be installed on or near the pump. The installation itself poses a challenge, but the real problem is that these sensors are not designed to operate underwater. Water damage, battery replacement and other sensor maintenance will require you to lift the pump — the last thing you can afford to do during drought season.
A technique called electrical signature analysis (ESA) was developed precisely to solve this issue. By measuring current and voltage instead of vibrations or temperature, you can install your sensors in the motor control cabinet (or anywhere else between the motor and the actual equipment it’s driving). ESA has proven to be as effective as vibration and thermal analysis in assessing machine health — both electrical and mechanical. It is particularly effective in detecting key borehole failure modes, such as clogging from chalk or iron buildup and electrical faults in the VFD or motor.
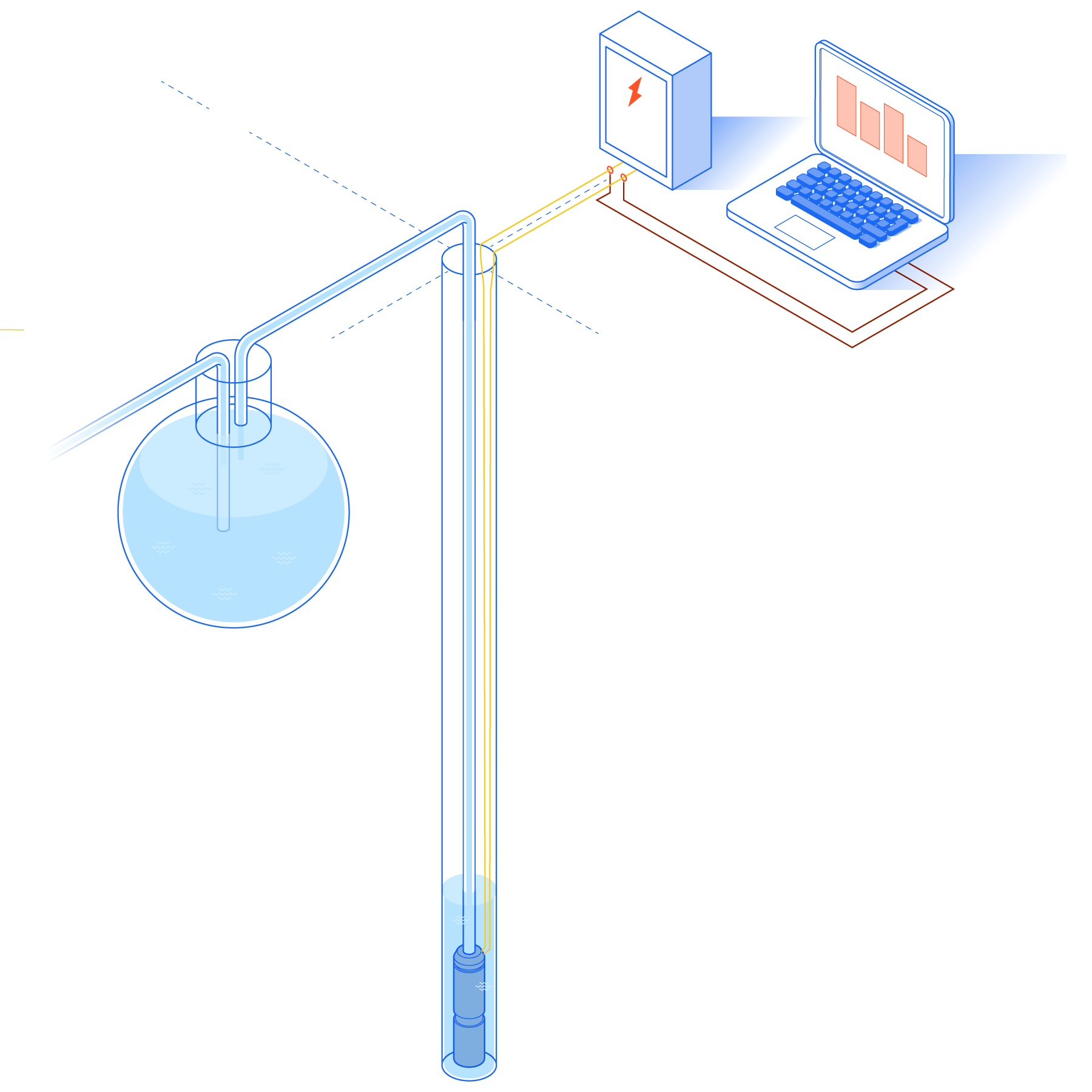
RELATED READING: An in-depth look at ESA’s strengths, weaknesses and fault detection accuracy on electric submersible pumps
Full health and energy intelligence
As the only reliable condition monitoring technique for submerged equipment, ESA is a no-brainer for borehole pumps — but it’s also a valuable addition to existing vibration, thermal or oil-based systems on other assets. A robust condition-based maintenance strategy should always use multiple monitoring technologies on critical equipment. By combining (for example) a vibration system and an ESA system, you increase the scope of faults you can detect. It only makes sense to do all you can to have full insight into the status and performance of your most critical lift, booster and distribution pumps.
ESA adds another benefit: energy intelligence. Because they measure electrical signals, ESA systems can directly tell you how your pumps are performing, so you can take steps to raise their efficiency. This can save significant money over an asset’s lifetime. What’s more, an efficient pump is a happy pump from the health perspective, too — so optimizing efficiency not only lowers total operating costs, but also extends the pump’s lifetime and reduces the chance of unexpected breakdown when you can least afford it.
RELATED READING: The path to Net Zero: improving energy efficiency in the water industry
Enter drought season prepared
Condition-based maintenance (CBM) is a powerful tool to help you proactively manage the risks of an upcoming drought. Make sure your drought response plan takes advantage of the benefits CBM offers in preventing interruptions to supply.
It takes time to install new technology, so start early. That way you can add ESA to your condition-based maintenance program where it makes the most sense, and go into drought season knowing you’ve got the best possible setup in place for those months when it’s critical to keep your network fully up and running.
If you’re just starting to explore condition-based maintenance, our quick-start guide is full of tips and worksheets to set up (and later scale up) a successful technology pilot.