For industries that rely on fluid movement—such as water treatment, oil and gas, agriculture, and manufacturing—pump failures are more than just an inconvenience. A single breakdown can cause costly downtime, disrupt entire operations, and lead to expensive repairs or even catastrophic system failures.
To keep pumps running efficiently, it’s crucial to understand why they fail in the first place. Recognizing early warning signs and implementing proactive maintenance strategies can significantly extend the lifespan of your equipment while ensuring smooth operations.
The most common causes of pump failure include:
- Mechanical seal leakage
- Bearing issues
- Impeller wear and tear
- Coupling-related issues
- Operational errors
- Power supply issues
6 common causes of pump failure
It’s crucial to keep pumps healthy, but to do that you need to answer one important question: why do pumps fail? The following reasons account for over 60% of pump failures, according to Grundfos:
1. Mechanical seal leakage
Most leakages usually take place at the interface between the two seal faces, but there are occasions when leakages also come from the secondary sealing area. There are a variety of reasons for mechanical seal leakage, such as dry running, thermal distortion and misalignment of seal rings, to name a few.
2. Bearing issues
According to the technical report by the RKB Bearing Industries Group, by far the most common reason for bearing failure is improper lubrication (80%), causing it to overheat. Other causes include improper bearing selection, overload, fatigue and many more.
3. Impeller wear and tear
As with other failures, there are multiple reasons for impeller wear and tear. One of the most common is erosion, but it can also result from an improperly sized pump, which can lead to an imbalance of pressure.
4. Coupling-related issues
Most frequently encountered coupling failures happen for the following reasons: misalignment, overload, uncommon environmental causes, torsional vibration and improper lubrication.
5. Operational errors
Even the most advanced pump won’t last if it’s run outside its intended parameters. Improper startup and shutdown, overloading, or ignoring manufacturer guidelines can lead to overheating, excessive wear, and dangerous malfunctions.
For submersible pumps, failing to maintain adequate submersion levels can cause dry running, leading to seal failure and motor burnout. The solution? Invest in operator training, implement automated controls, and monitor system data to prevent costly mistakes.
6. Power supply issues
A stable power supply is critical for pump performance. Voltage fluctuations, power surges, and unexpected outages can wreak havoc on motors, causing them to overheat, operate inefficiently, or fail altogether.
Submersible pumps are especially vulnerable due to their reliance on electrical insulation in wet environments. Electrical Signature Analysis (ESA) can detect current anomalies before they cause failure, while surge protectors, backup power systems, and routine electrical inspections provide an extra layer of protection.
The fastest fix is to replace the failed component, but that doesn’t address the underlying issue. Pumps can fail due to multiple contributing factors. For example, if a pump isn’t properly grounded, current can leak into a bearing and damage it. Similarly, cavitation can wear down seals, bearings, and impellers over time. Replacing damaged parts may restore function temporarily, but without addressing root causes—such as grounding issues or cavitation—the failures will continue.
To prevent recurring failures, it’s important to detect these underlying issues before they escalate. Condition monitoring technologies can help identify problems early, allowing for proactive maintenance and reducing costly downtime.
How to detect early signs of pump failure
Pump failures don’t happen overnight—there are always warning signs that, if caught early, can prevent costly downtime and repairs.
Key warning signs to watch for:
- Unusual noises – Grinding, whining, or banging sounds often signal cavitation, worn bearings, or misalignment.
- Excessive vibration – Increased shaking can indicate misaligned shafts, imbalanced impellers, or failing bearings.
- Reduced flow or pressure – A sudden drop in output may be caused by blockages, air leaks, or internal wear. In the video below
- Overheating – Motors or bearings running hotter than usual suggest poor lubrication, overloading, or electrical issues.
- Leaks or seal damage – Visible leaks often point to worn-out seals or excessive internal pressure.
- Erratic power consumption – Spikes in energy use can indicate an inefficient or struggling pump.
Routine inspections, vibration analysis, and thermal monitoring can help detect these issues before they lead to complete failure. Investing in predictive maintenance tools like Electrical Signature Analysis (ESA) or IoT-based condition monitoring can reduce downtime and repair costs.
How does a condition monitoring system track down potential failures in pumps before they happen?
A condition monitoring system works by keeping a close eye on a pump’s vital signs—things like vibrations, temperature, and noise. When something starts to go wrong, these signals change in subtle but telling ways. Think of it like a doctor listening to your heartbeat; an unusual rhythm could hint at a problem before you even feel sick.
By analyzing these shifts, the system can spot early warning signs of wear, misalignment, or other issues long before they turn into full-blown failures. Different monitoring techniques specialize in detecting different kinds of faults, some catching problems sooner than others. The right approach depends on what you need to monitor, the environment your pumps operate in, and how critical they are to your process.
Common methods include vibration analysis, oil analysis, infrared thermography, electrical signature analysis, and acoustic emissions—each with its own strengths when it comes to preventing costly breakdowns.
Pump failure analysis: Techniques for pump failure diagnosis and prevention
Effective pump failure management requires both diagnostic and preventive techniques. Diagnostic methods help identify the root cause of failures, while preventive techniques focus on monitoring performance trends to detect early warning signs before a breakdown occurs. Combining these approaches ensures better reliability, fewer emergency repairs, and lower maintenance costs.
Diagnostic techniques: identifying and understanding failures
Root Cause Analysis (RCA)
When a pump fails, understanding the underlying cause is crucial to prevent recurrence. Root Cause Analysis (RCA) is a structured approach that examines performance data, maintenance records, and operational conditions to determine what led to the failure. Two widely used methods are Failure Mode and Effects Analysis (FMEA), which identifies potential failure points and their consequences, and Fault Tree Analysis (FTA), which systematically traces failure pathways to their root cause. By diagnosing recurring issues, RCA helps maintenance teams develop targeted corrective actions.
Electrical Signature Analysis (ESA)
Electrical Signature Analysis (ESA) is a powerful tool for detecting both electrical and mechanical issues in pumps by analyzing motor current and voltage signals. This method is particularly effective for submersible pumps, as it can identify problems that are otherwise difficult to detect, such as winding insulation breakdown, phase imbalances, mechanical misalignments, and rotor bar defects. Since ESA provides early warnings, it allows maintenance teams to intervene before these issues result in pump failure.
Vibration Analysis (VA)
Changes in vibration patterns can indicate mechanical problems in a pump, making Vibration Analysis (VA) a key diagnostic tool. Unusual vibrations often signal misalignment, imbalance, bearing wear, or cavitation—all of which can lead to serious damage if left unchecked. By continuously monitoring vibration frequencies, maintenance teams can detect abnormalities early and take corrective action before minor issues escalate into full pump failures.
Wear Debris Analysis (WDA)
When internal components of a pump begin to wear down, they release tiny metal particles into the lubrication system. Wear Debris Analysis (WDA) examines these particles to determine the type of wear, the affected component, and the severity of the damage. Techniques such as ferrography and spectroscopy help classify wear patterns, distinguishing between adhesive, abrasive, and fatigue wear. This information allows maintenance teams to detect potential failures before they cause significant damage.
Preventive techniques: Detecting early warning signs
Thermographic inspection
Abnormal heat buildup is often an early indicator of pump failure. Thermographic inspection uses infrared imaging to detect hot spots in components such as bearings, seals, and motor windings, which can indicate lubrication issues, excessive friction, or electrical faults. By identifying overheating parts before they fail, thermal inspections help prevent unexpected breakdowns and extend the life of critical pump components.
Oil and lubricant analysis
The condition of a pump’s lubrication system is a key factor in its overall reliability. Regular oil and lubricant analysis helps detect contaminants such as metal particles, water, and sludge, which can indicate early signs of component wear or environmental contamination. Changes in viscosity, acidity, or the presence of wear debris provide valuable insights into the health of bearings, gears, and seals. By continuously monitoring lubricant condition, maintenance teams can take preventive action to reduce wear and extend the lifespan of pump components.
Pump Performance Monitoring (PPM)
Instead of waiting for failure symptoms to appear, Pump Performance Monitoring (PPM) allows operators to track key performance parameters in real time. By monitoring flow rate, pressure, temperature, and power consumption, deviations from baseline data can indicate potential efficiency losses, blockages, or mechanical degradation. Implementing a remote monitoring system with real-time analytics provides early detection of performance issues, helping water utilities optimize pump efficiency and avoid costly downtime.
Why a combined approach matters
Understanding why pumps fail and identifying early warning signs before failures occur are both essential for maintaining pump reliability. Diagnostic techniques like RCA, ESA, and Vibration Analysis help determine the cause of failures, while preventive approaches like PPM, thermographic inspection, and lubricant analysis provide real-time insights into pump health. Using a combination of these methods allows for more efficient maintenance planning, reducing the risk of unplanned outages and lowering long-term operational costs.
Failure modes specific to electrical submersible pumps (ESP)
While all pumps face common failure risks, Electrical Submersible Pumps (ESP) are particularly vulnerable due to their submerged operation and intricate design. These factors introduce unique failure modes that require specialized monitoring and mitigation strategies. Below are some of the most common ESP-specific vulnerabilities and how to address them.
Insulation degradation and electrical failures
Since ESPs function underwater, insulation integrity plays a major role in preventing electrical faults. Over time, exposure to high temperatures, moisture infiltration, and mechanical stress can weaken insulation, increasing the risk of short circuits and motor failure. Conducting insulation resistance tests at regular intervals helps identify early-stage deterioration before it leads to downtime.
Gas locking
In oil and gas applications, ESPs are prone to gas locking, a condition where excessive free gas in the pumped fluid disrupts flow through the impellers. This results in lost efficiency, overheating, and potential damage. To combat gas locking, operators can install gas separators and adjust intake designs to improve fluid handling.
Seal failure and water ingress
Mechanical seals prevent external fluids from entering the motor. However, factors like wear, pressure fluctuations, and temperature changes can cause seal deterioration, leading to water intrusion and electrical malfunctions. Regular seal inspections and using pressure-equalizing devices can enhance seal longevity and reduce failure risks.
Sand and solids abrasion
ESPs in deep-well and oilfield applications often operate in environments containing high levels of sand and abrasive particles. These materials accelerate wear on impellers, diffusers, and bearings, gradually reducing pump efficiency. Utilizing hardened components, sand screens, and variable-speed drives helps minimize wear and extend pump lifespan.
By addressing these ESP-specific vulnerabilities, operators can enhance performance, minimize unexpected failures, and extend equipment longevity.
Why is Electrical Signature Analysis (ESA) the best way to monitor submersible pumps?
Submersible pumps operate in harsh and inaccessible environments, making traditional diagnostic methods like vibration analysis and thermographic inspection more challenging to implement.
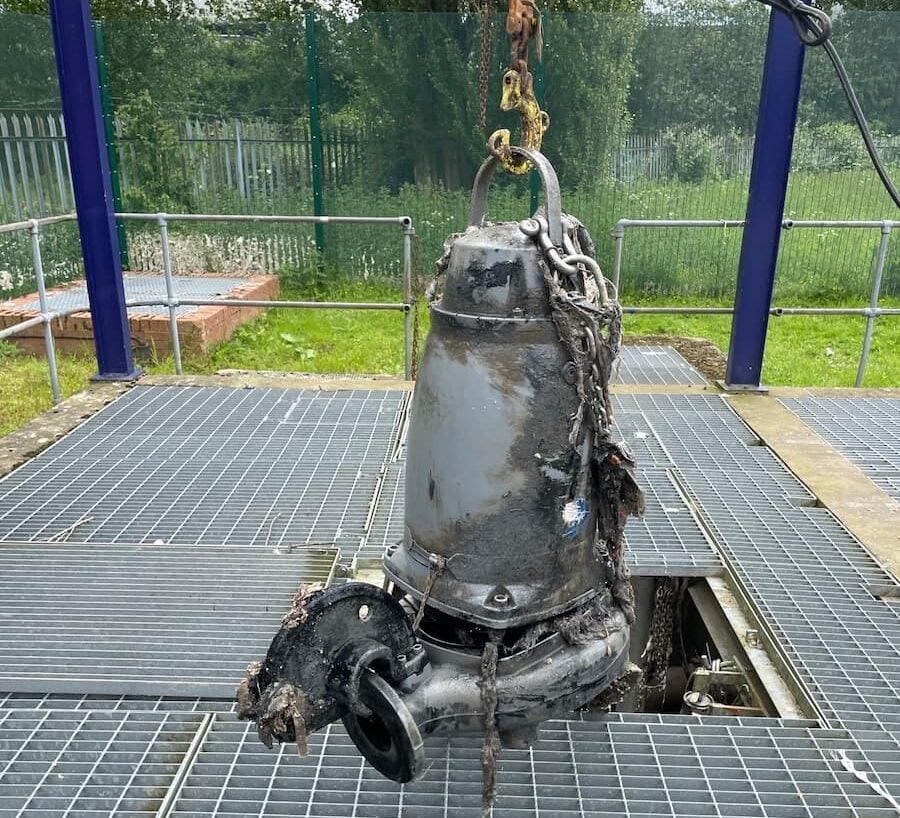
Electrical Signature Analysis (ESA) is the most effective and practical approach for monitoring the condition of submersible pumps due to the following reasons:
Non-intrusive monitoring
ESA analyzes electrical signals (current and voltage) from the motor without requiring physical access to the pump. Since submersible pumps are often located underwater, in wells, or in hazardous areas, accessing them for vibration or thermal measurements is difficult and costly. ESA provides a remote, non-intrusive way to monitor pump health without disrupting operations.
Early detection of mechanical and electrical Issues
ESA can detect faults before they manifest into catastrophic failures. By analyzing deviations in electrical waveforms, ESA identifies early signs of:
- Winding insulation breakdown – leading to motor overheating and short circuits.
- Phase imbalances and voltage fluctuations – causing inefficient motor operation and premature failure.
- Rotor bar defects – indicating potential degradation in motor components.
- Mechanical misalignments and bearing wear – detected through irregular motor current variations, which correlate with mechanical stress.
Detection of pump load and flow irregularities
Unlike vibration analysis, which primarily focuses on mechanical aspects, ESA can diagnose issues related to pump load variations and flow problems. Changes in electrical current signatures often indicate:
- Cavitation – characterized by irregular load fluctuations and motor instability.
- Blockages in suction or discharge lines – reflected in abnormal motor current draw.
- Seal and impeller wear – increasing power consumption due to rising friction or inefficiencies.
Electrical Signature Analysis works in any environment
Since ESA relies on electrical signal analysis rather than physical sensor readings, it is unaffected by extreme temperatures, high-pressure environments, or submersion in liquids. This makes it ideal for deep wells, wastewater systems, offshore applications, and other difficult-to-access installations.
Cost-effective and scalable
Beyond its diagnostic accuracy, ESA is a highly scalable and cost-efficient solution for pump monitoring. Unlike traditional methods that require sensor placement directly on the asset, ESA provides remote insights from the motor control cabinet. This makes it particularly valuable for industries operating multiple submersible pumps in hard-to-reach locations.
With ESA, operators can:
- Eliminate the need for physical sensors on the pump – Unlike vibration or temperature monitoring, ESA does not require additional sensors directly installed on the submerged pump.
- Monitor pumps remotely – ESA integrates with IoT-based condition monitoring systems, enabling real-time data analysis and predictive maintenance without manual inspections.
- Reduce downtime and emergency repairs – By predicting failures in advance, ESA minimizes unexpected breakdowns and optimizes maintenance schedules.
Conclusion
Preventing pump failures requires a shift from routine fixes to strategic, condition-based maintenance. With tools like Electrical Signature Analysis (ESA), vibration monitoring, and oil analysis, maintenance teams can catch problems early, reduce unplanned downtime, and extend equipment lifespan.
Instead of reacting to breakdowns, industries can build reliability into their systems by leveraging real-time data and predictive diagnostics. This approach not only improves performance but also lowers costs and ensures smooth, uninterrupted operations.
FAQs about pump failures:
How long should a pump last before failure?
The lifespan of a pump depends on operating conditions, maintenance frequency, and pump type, but most pumps last 5–15 years with proper care.
Why is my pump making unusual noises?
Strange noises can be caused by cavitation, air leaks, worn bearings, impeller damage, or misalignment.
Why is my pump vibrating excessively?
Excessive vibration is usually due to shaft misalignment, imbalance, cavitation, worn bearings, or improper installation.
What causes seal failure in pumps?
Worn-out seals, excessive pressure, misalignment, temperature fluctuations, or contamination can cause seals to fail, leading to leaks.
Are submersible pumps more prone to failure?
Yes, because they operate underwater in extreme conditions, making them more vulnerable to seal failure, water ingress, electrical issues, and insulation breakdown.
What is the best way to monitor pump health remotely?
Electrical Signature Analysis (ESA), vibration monitoring, and IoT-based condition monitoring allow for real-time, remote pump diagnostics.
What type of maintenance schedule should I follow to prevent pump failure?
A preventive maintenance schedule should include regular inspections, lubrication, seal checks, vibration analysis, and thermal imaging at monthly, quarterly, and annual intervals.