Para las industrias que dependen del movimiento de fluidos, como las de tratamiento de aguas, petróleo y gas, agricultura y fabricación, los fallos de las bombas son algo más que un inconveniente. Una sola avería puede causar costosos tiempos de inactividad, interrumpir operaciones enteras y provocar costosas reparaciones o incluso fallos catastróficos del sistema.
Para que las bombas sigan funcionando con eficacia, es fundamental entender por qué fallan. Reconocer las primeras señales de advertencia y aplicar medidas proactivas estrategias de mantenimiento puede prolongar significativamente la vida útil de sus equipos, garantizando al mismo tiempo un funcionamiento sin problemas.
Las causas más comunes de avería de las bombas son
- Fugas en los cierres mecánicos
- Problemas de rodamientos
- Desgaste del impulsor
- Problemas de acoplamiento
- Errores operativos
- Problemas de alimentación
6 causas habituales de avería de las bombas
Es crucial mantener las bombas en buen estado, pero para ello hay que responder a una pregunta importante: ¿por qué fallan las bombas? Las siguientes razones explican más del 60% de las averías de bombas, según Grundfos:
1. Fugas en cierres mecánicos
La mayoría de las fugas suelen producirse en la interfaz entre las dos caras del cierre, pero hay ocasiones en las que las fugas también proceden de la zona de estanquidad secundaria. Las fugas de los cierres mecánicos pueden deberse a diversos motivos, como el funcionamiento en seco, la distorsión térmica y la desalineación de los anillos de estanquidad, por citar algunos..
2. Cuestiones de rodamiento
Según el informe técnico por el Grupo RKB Bearing IndustriesLa causa más común de fallo de los rodamientos es, con diferencia, una lubricación inadecuada (80%), que provoca su sobrecalentamiento. Otras causas son la selección inadecuada del rodamiento, la sobrecarga, la fatiga y muchas más.
3. Desgaste del impulsor
Al igual que ocurre con otras averías, el desgaste del impulsor puede deberse a múltiples causas. Una de las más comunes es la erosión, pero también puede ser el resultado de una bomba de tamaño inadecuado, lo que puede provocar un desequilibrio de la presión.
4. Cuestiones relacionadas con el acoplamiento
Los fallos de acoplamiento más frecuentes se producen por las siguientes razones: desalineación, sobrecarga, causas ambientales poco comunes, vibración torsional y lubricación inadecuada.
5. Errores operativos
Incluso la bomba más avanzada no durará mucho si funciona fuera de los parámetros previstos. La puesta en marcha y el apagado incorrectos, la sobrecarga o el incumplimiento de las directrices del fabricante pueden provocar sobrecalentamiento, desgaste excesivo y averías peligrosas.
En el caso de las bombas sumergibles, si no se mantienen unos niveles de inmersión adecuados, puede producirse un funcionamiento en seco que provoque el fallo de las juntas y la rotura del motor. ¿Cuál es la solución? Invertir en la formación de los operarios, implantar controles automatizados y supervisar los datos del sistema para evitar errores costosos.
6. Problemas de alimentación
Un suministro eléctrico estable es fundamental para el rendimiento de las bombas. Las fluctuaciones de tensión, las subidas de tensión y los cortes de suministro inesperados pueden causar estragos en los motores, provocando su sobrecalentamiento, un funcionamiento ineficiente o un fallo total.
Las bombas sumergibles son especialmente vulnerables debido a su dependencia del aislamiento eléctrico en entornos húmedos. Análisis de firmas eléctricas (ESA) pueden detectar anomalías de la corriente antes de que provoquen fallos, mientras que los protectores contra sobretensiones, los sistemas de alimentación de reserva y las inspecciones eléctricas rutinarias proporcionan una capa adicional de protección.
La solución más rápida es sustituir el componente averiado, pero eso no soluciona el problema de fondo. Las bombas pueden fallar debido a múltiples factores. Por ejemplo, si una bomba no está bien conectada a tierra, puede entrar corriente en un cojinete y dañarlo. Del mismo modo, la cavitación puede desgastar juntas, cojinetes e impulsores con el paso del tiempo. La sustitución de las piezas dañadas puede restablecer el funcionamiento temporalmente, pero si no se abordan las causas fundamentales, como los problemas de conexión a tierra o la cavitación, los fallos continuarán.
Para evitar fallos recurrentes, es importante detectar estos problemas subyacentes antes de que se agraven. Monitoreo de condiciones pueden ayudar a detectar los problemas en una fase temprana, lo que permite realizar un mantenimiento proactivo y reducir los costosos tiempos de inactividad.
Cómo detectar los primeros signos de fallo de una bomba
Las averías de las bombas no se producen de la noche a la mañana: siempre hay señales de advertencia que, si se detectan a tiempo, pueden evitar costosos tiempos de inactividad y reparaciones.
Principales señales de alerta:
- Ruidos inusuales - Los chirridos, silbidos o golpes suelen indicar cavitación, rodamientos desgastados o desalineación.
- Vibración excesiva - Un aumento de las sacudidas puede indicar ejes desalineados, impulsores desequilibrados o cojinetes defectuosos.
- Caudal o presión reducidos - Una caída repentina de la potencia puede deberse a obstrucciones, fugas de aire o desgaste interno. En el siguiente vídeo
- Sobrecalentamiento - Los motores o cojinetes que se calientan más de lo normal sugieren una lubricación deficiente, sobrecarga o problemas eléctricos.
- Fugas o daños en las juntas - Las fugas visibles suelen indicar juntas desgastadas o una presión interna excesiva.
- Consumo de energía errático - Los picos en el consumo de energía pueden indicar una bomba ineficiente o con problemas.
Inspecciones rutinarias, análisis de vibracionesy la monitorización térmica pueden ayudar a detectar estos problemas antes de que provoquen un fallo completo. Invertir en herramientas de mantenimiento predictivo como el análisis de firmas eléctricas (ESA) o la monitorización de estado basada en IoT puede reducir el tiempo de inactividad y los costes de reparación.
¿Cómo detecta un sistema de monitorización de estado los posibles fallos de las bombas antes de que se produzcan?
Un sistema de monitorización de estado vigila de cerca las constantes vitales de una bomba, como las vibraciones, la temperatura y el ruido. Cuando algo empieza a ir mal, estas señales cambian de forma sutil pero reveladora. Piense en ello como si un médico escuchara los latidos de su corazón; un ritmo inusual podría indicar un problema incluso antes de que se sienta enfermo.
Al analizar estos cambios, el sistema puede detectar señales tempranas de desgaste, desalineación u otros problemas mucho antes de que se conviertan en fallos totales. Las distintas técnicas de control se especializan en la detección de diferentes tipos de fallos, y algunas detectan los problemas antes que otras. El enfoque adecuado depende de lo que necesite supervisar, del entorno en el que operen sus bombas y de lo importantes que sean para su proceso.
Métodos comunes incluyen análisis de vibraciones, análisis del aceiteLa termografía por infrarrojos, el análisis de la firma eléctrica y las emisiones acústicas, cada uno con sus propias ventajas a la hora de evitar averías costosas.
Análisis de averías de bombas: Técnicas de diagnóstico y prevención de fallos de bombas
Una gestión eficaz de las averías de las bombas requiere técnicas tanto de diagnóstico como de prevención. Los métodos de diagnóstico ayudan a identificar la causa raíz de las averías, mientras que las técnicas preventivas se centran en supervisar las tendencias de rendimiento para detectar señales de advertencia tempranas antes de que se produzca una avería. La combinación de estos enfoques garantiza una mayor fiabilidad, menos reparaciones de emergencia y menores costes de mantenimiento.
Técnicas de diagnóstico: identificar y comprender los fallos
Análisis de Causas Raíz (ACR)
Cuando una bomba falla, es crucial comprender la causa subyacente para evitar que se repita. El análisis de causa raíz (ACR) es un método estructurado que examina los datos de rendimiento, los registros de mantenimiento y las condiciones de funcionamiento para determinar qué provocó el fallo. Dos métodos muy utilizados son el Análisis Modal de Fallos y Efectos (AMFE), que identifica posibles puntos de fallo y sus consecuencias, y el Análisis del Árbol de Fallos (AEF), que rastrea sistemáticamente las vías de fallo hasta su causa raíz. Al diagnosticar problemas recurrentes, el ACR ayuda a los equipos de mantenimiento a desarrollar acciones correctivas específicas.
Análisis de firmas eléctricas (ESA)
El análisis de firmas eléctricas (ESA) es una potente herramienta para detectar problemas eléctricos y mecánicos en bombas mediante el análisis de las señales de corriente y tensión del motor. Este método es especialmente eficaz para bombas sumergibles, ya que puede identificar problemas que de otro modo serían difíciles de detectar, como la rotura del aislamiento del bobinado, desequilibrios de fase, desajustes mecánicos y defectos en la barra del rotor. Dado que el ESA proporciona alertas tempranas, permite a los equipos de mantenimiento intervenir antes de que estos problemas provoquen el fallo de la bomba.
Análisis de vibraciones (VA)
Los cambios en los patrones de vibración pueden indicar problemas mecánicos en una bomba, por lo que el análisis de vibraciones (AV) es una herramienta de diagnóstico clave. Las vibraciones inusuales suelen indicar desalineación, desequilibrio, desgaste de los cojinetes o cavitación, todo lo cual puede provocar daños graves si no se controla. Mediante la supervisión continua de las frecuencias de vibración, los equipos de mantenimiento pueden detectar anomalías a tiempo y tomar medidas correctivas antes de que los problemas menores se conviertan en fallos totales de la bomba.
Análisis de residuos de desgaste (WDA)
Cuando los componentes internos de una bomba empiezan a desgastarse, liberan diminutas partículas metálicas en el sistema de lubricación. El análisis de residuos de desgaste (WDA) examina estas partículas para determinar el tipo de desgaste, el componente afectado y la gravedad del daño. Técnicas como la ferrografía y la espectroscopia ayudan a clasificar los patrones de desgaste, distinguiendo entre desgaste adhesivo, abrasivo y por fatiga. Esta información permite a los equipos de mantenimiento detectar posibles fallos antes de que causen daños importantes.
Técnicas preventivas: Detección de los primeros signos de alerta
Inspección termográfica
La acumulación anormal de calor suele ser un indicador precoz de avería en una bomba. La inspección termográfica utiliza imágenes por infrarrojos para detectar puntos calientes en componentes como cojinetes, juntas y bobinados de motores, que pueden indicar problemas de lubricación, fricción excesiva o fallos eléctricos. Al identificar las piezas sobrecalentadas antes de que fallen, las inspecciones termográficas ayudan a evitar averías inesperadas y a prolongar la vida útil de los componentes críticos de las bombas.
Análisis de aceites y lubricantes
El estado del sistema de lubricación de una bomba es un factor clave para su fiabilidad general. Los análisis periódicos de aceite y lubricante ayudan a detectar contaminantes como partículas metálicas, agua y lodos, que pueden indicar signos tempranos de desgaste de los componentes o contaminación ambiental. Los cambios en la viscosidad, la acidez o la presencia de residuos de desgaste proporcionan información valiosa sobre el estado de los rodamientos, engranajes y juntas. Mediante la supervisión continua del estado del lubricante, los equipos de mantenimiento pueden tomar medidas preventivas para reducir el desgaste y prolongar la vida útil de los componentes de la bomba.
Control del rendimiento de las bombas (PPM)
En lugar de esperar a que aparezcan los síntomas de un fallo, la supervisión del rendimiento de las bombas (PPM) permite a los operarios realizar un seguimiento en tiempo real de los principales parámetros de rendimiento. Mediante la supervisión del caudal, la presión, la temperatura y el consumo eléctrico, las desviaciones de los datos de referencia pueden indicar posibles pérdidas de eficiencia, bloqueos o degradación mecánica. La implantación de un sistema de monitorización remota con análisis en tiempo real permite detectar con antelación los problemas de rendimiento, lo que ayuda a las empresas de suministro de agua a optimizar la eficiencia de las bombas y evitar costosos tiempos de inactividad.
Por qué es importante un enfoque combinado
Comprender por qué fallan las bombas e identificar las señales de advertencia antes de que se produzcan los fallos es esencial para mantener la fiabilidad de las bombas. Técnicas de diagnóstico como RCA, ESA y análisis de vibraciones ayudan a determinar la causa de los fallos, mientras que métodos preventivos como PPM, inspección termográfica y análisis de lubricantes proporcionan información en tiempo real sobre el estado de las bombas. El uso de una combinación de estos métodos permite una planificación más eficaz del mantenimiento, reduciendo el riesgo de paradas imprevistas y disminuyendo los costes operativos a largo plazo.
Modos de fallo específicos de las bombas eléctricas sumergibles (ESP)
Aunque todas las bombas se enfrentan a riesgos de avería comunes, las bombas eléctricas sumergibles (BES) son especialmente vulnerables debido a su funcionamiento sumergido y a su intrincado diseño. Estos factores introducen modos de fallo únicos que requieren seguimiento especializado y estrategias de mitigación. A continuación se detallan algunas de las vulnerabilidades específicas de ESP más comunes y cómo solucionarlas.
Degradación del aislamiento y fallos eléctricos
Dado que los ESP funcionan bajo el agua, la integridad del aislamiento desempeña un papel fundamental en la prevención de fallos eléctricos. Con el tiempo, la exposición a altas temperaturas, la infiltración de humedad y los esfuerzos mecánicos pueden debilitar el aislamiento, aumentando el riesgo de cortocircuitos y averías del motor. Realizar pruebas de resistencia del aislamiento a intervalos regulares ayuda a identificar el deterioro en una fase temprana antes de que provoque tiempos de inactividad.
Bloqueo de gas
En las aplicaciones de petróleo y gas, los ESP son propensos al bloqueo por gas, una situación en la que un exceso de gas libre en el fluido bombeado interrumpe el flujo a través de los impulsores. El resultado es una pérdida de eficacia, sobrecalentamiento y posibles daños. Para combatir el bloqueo por gas, los operadores pueden instalar gcomo separadores y ajustar los diseños de admisión para mejorar el manejo de fluidos.
Rotura de juntas y entrada de agua
Las juntas mecánicas impiden la entrada de fluidos externos en el motor. Sin embargo, factores como el desgaste, las fluctuaciones de presión y los cambios de temperatura pueden deteriorar las juntas y provocar la entrada de agua y fallos eléctricos. Las inspecciones periódicas de los sellos y el uso de dispositivos de igualación de presión pueden aumentar la longevidad de los sellos y reducir los riesgos de avería.
Abrasión de arena y sólidos
Los sistemas ESP en aplicaciones de pozos profundos y yacimientos petrolíferos operan a menudo en entornos que contienen altos niveles de arena y partículas abrasivas. Estos materiales aceleran el desgaste de impulsores, difusores y cojinetes, reduciendo gradualmente la eficacia de la bomba. La utilización de componentes endurecidos, filtros de arena y variadores de velocidad ayuda a minimizar el desgaste y a prolongar la vida útil de la bomba.
Al abordar estas vulnerabilidades específicas de los ESP, los operadores pueden mejorar el rendimiento, minimizar los fallos inesperados y prolongar la longevidad de los equipos.
¿Por qué el análisis de firmas eléctricas (ESA) es la mejor forma de supervisar las bombas sumergibles?
Las bombas sumergibles funcionan en entornos difíciles e inaccesibles, lo que dificulta la aplicación de métodos de diagnóstico tradicionales como el análisis de vibraciones y la inspección termográfica.
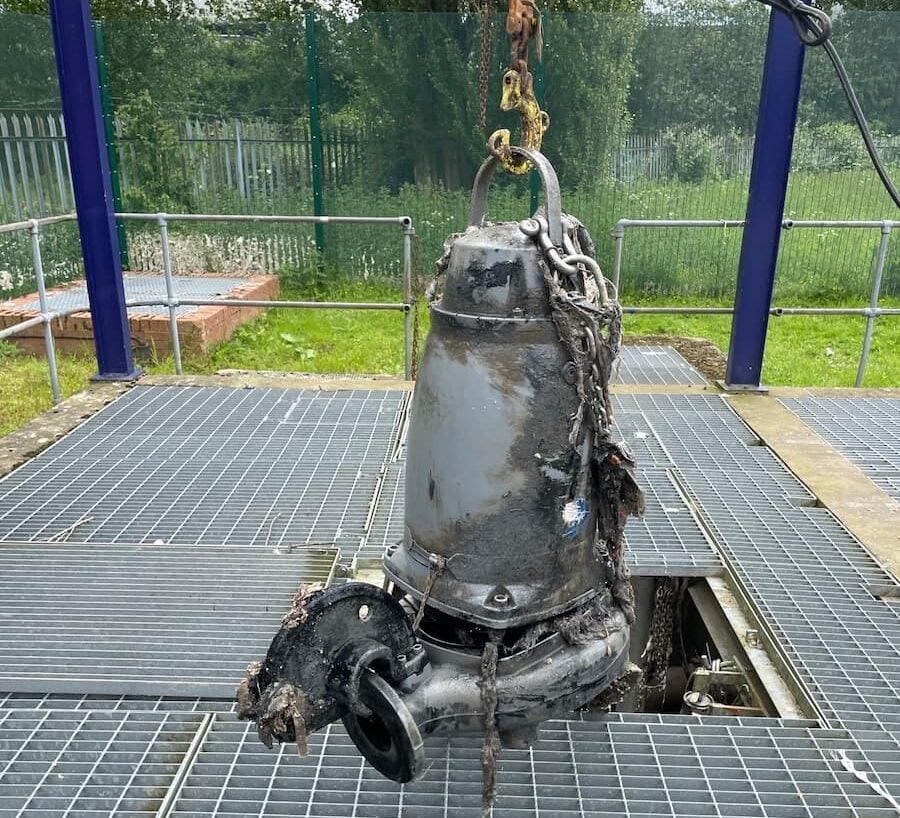
El análisis de firmas eléctricas (ESA) es el método más eficaz y práctico para controlar el estado de las bombas sumergibles por las siguientes razones:
Vigilancia no intrusiva
ESA analiza las señales eléctricas (corriente y tensión) del motor sin necesidad de acceder físicamente a la bomba. Dado que las bombas sumergibles suelen estar situadas bajo el agua, en pozos o en zonas peligrosas, acceder a ellas para realizar mediciones térmicas o de vibraciones resulta difícil y costoso. ESA ofrece una forma remota y no intrusiva de supervisar el estado de las bombas sin interrumpir su funcionamiento.
Detección precoz de problemas mecánicos y eléctricos
La ESA puede detectar fallos antes de que se manifiesten en averías catastróficas. Mediante el análisis de las desviaciones en las formas de onda eléctricas, ESA identifica signos tempranos de:
- Rotura del aislamiento del bobinado - provocando el sobrecalentamiento del motor y cortocircuitos.
- Desequilibrios de fase y fluctuaciones de tensión - causando un funcionamiento ineficaz del motor y un fallo prematuro.
- Defectos de la barra del rotor - lo que indica una posible degradación de los componentes del motor.
- Desajustes mecánicos y desgaste de los rodamientos - detectadas a través de variaciones irregulares de la corriente del motor, que se correlacionan con el estrés mecánico.
Detección de irregularidades en la carga y el caudal de la bomba
A diferencia del análisis de vibraciones, que se centra principalmente en aspectos mecánicos, el ESA puede diagnosticar problemas relacionados con variaciones de carga de la bomba y problemas de caudal. Los cambios en las firmas de corriente eléctrica suelen indicar:
- Cavitación - caracterizada por fluctuaciones irregulares de la carga e inestabilidad del motor.
- Obstrucciones en los conductos de aspiración o descarga - reflejado en un consumo anormal de corriente del motor.
- Desgaste de la junta y el impulsor - aumento del consumo de energía debido al aumento de la fricción o a ineficiencias.
El análisis de firmas eléctricas funciona en cualquier entorno
Dado que la ESA se basa en el análisis de señales eléctricas en lugar de en las lecturas físicas de los sensores, no se ve afectada por temperaturas extremas, entornos de alta presión ni la inmersión en líquidos. Por eso es ideal para pozos profundos, sistemas de aguas residuales, aplicaciones marinas y otras instalaciones de difícil acceso.
Rentable y ampliable
Más allá de su precisión diagnóstica, la ESA es un altamente escalable y rentable para la supervisión de bombas. A diferencia de los métodos tradicionales que requieren la colocación de sensores directamente en el activo, ESA proporciona percepciones remotas desde el armario de control del motor. Esto lo hace especialmente valioso para las industrias que operan múltiples bombas sumergibles en lugares de difícil acceso.
Con ESA, los operadores pueden:
- Elimina la necesidad de sensores físicos en la bomba - A diferencia de la supervisión de las vibraciones o la temperatura, la ESA no requiere sensores adicionales instalados directamente en la bomba sumergida.
- Supervise las bombas a distancia - ESA se integra con sistemas de monitorización de estado basados en IoT, lo que permite el análisis de datos en tiempo real y el mantenimiento predictivo sin inspecciones manuales.
- Reduzca el tiempo de inactividad y las reparaciones de emergencia - Al predecir los fallos con antelación, la ESA minimiza las averías inesperadas y optimiza los programas de mantenimiento.
Conclusión
Prevenir las averías de las bombas exige pasar de las reparaciones rutinarias al mantenimiento estratégico basado en el estado. Con herramientas como Análisis de firmas eléctricas (ESA), control de vibraciones y análisis de aceiteLos equipos de mantenimiento pueden detectar los problemas a tiempo, reducir los tiempos de inactividad imprevistos y prolongar la vida útil de los equipos.
En lugar de reaccionar ante las averías, las industrias pueden incorporar fiabilidad a sus sistemas aprovechando los datos en tiempo real y el diagnóstico predictivo. Este enfoque no solo mejora el rendimiento, sino que también reduce los costes y garantiza un funcionamiento fluido e ininterrumpido.
Preguntas frecuentes sobre averías de bombas:
¿Cuánto debe durar una bomba antes de averiarse?
La vida útil de una bomba depende de las condiciones de funcionamiento, la frecuencia de mantenimiento y el tipo de bomba, pero la mayoría de las bombas duran entre 5 y 15 años con los cuidados adecuados.
¿Por qué mi bomba hace ruidos extraños?
Los ruidos extraños pueden deberse a cavitación, fugas de aire, cojinetes desgastados, daños en el impulsor o desalineación.
¿Por qué vibra excesivamente mi bomba?
Las vibraciones excesivas suelen deberse a una desalineación del eje, desequilibrio, cavitación, rodamientos desgastados o instalación incorrecta.
¿Cuáles son las causas de los fallos de estanqueidad en las bombas?
Las juntas desgastadas, la presión excesiva, la desalineación, las fluctuaciones de temperatura o la contaminación pueden provocar fallos en las juntas y fugas.
¿Son las bombas sumergibles más propensas a averiarse?
Sí, porque funcionan bajo el agua en condiciones extremas, lo que las hace más vulnerables a los fallos de estanqueidad, la entrada de agua, los problemas eléctricos y la rotura del aislamiento.
¿Cuál es la mejor manera de controlar a distancia el estado de la bomba?
El análisis de firmas eléctricas (ESA), la supervisión de vibraciones y la supervisión del estado basada en IoT permiten realizar diagnósticos remotos de las bombas en tiempo real.
¿Qué tipo de programa de mantenimiento debo seguir para evitar averías en la bomba?
Un programa de mantenimiento preventivo debe incluir inspecciones periódicas, lubricación, comprobación de juntas, análisis de vibraciones e imágenes térmicas a intervalos mensuales, trimestrales y anuales.