Análisis de firmas eléctricas
Los tiempos de inactividad imprevistos cuestan miles de millones al año a las industrias, interrumpen las operaciones y afectan gravemente a la rentabilidad. Análisis de firmas eléctricas (ESA) ofrece un enfoque proactivo de las máquinas monitoreo de la condiciónayudando a las organizaciones a detectar problemas en una fase temprana, minimizar los tiempos de inactividad imprevistos y mejorar la fiabilidad.
En este blog se explica qué es el ESA, cómo funciona, los fallos que puede detectar y cómo se compara con otros sistemas. técnicas de monitorización del estado. También estudiaremos sus ventajas, sus aplicaciones reales y por qué es una herramienta valiosa para la sociedad moderna. estrategias de mantenimiento.
¿Qué es el análisis de firmas eléctricas (ESA)?
El análisis de firmas eléctricas (ESA) es una técnica no intrusiva de supervisión del estado que utiliza la corriente y la tensión para detectar cambios sutiles en el funcionamiento de una máquina. Estos cambios pueden indicar fallos potenciales, dándole tiempo para programar el mantenimiento antes de que se produzca el fallo.
La ESA difiere de otras técnicas de control de estado, como las siguientes análisis de vibraciones o los sistemas basados en la temperatura, que dependen de sensores colocados directamente en el equipo. En cambio, el ESA supervisa los datos eléctricos a distancia, analizando cómo afecta el funcionamiento del motor conectado a su campo magnético y, posteriormente, a la corriente y la tensión. Esto lo hace especialmente útil para supervisar máquinas en entornos peligrosos o de difícil acceso.
Orígenes y evolución de la AEE
El Análisis de Firmas Eléctricas (ESA) se remonta a 1985, cuando el Laboratorio Nacional de Oak Ridge desarrolló Análisis de la firma de corriente del motor (MCSA) para supervisar de forma no intrusiva las válvulas accionadas por motor en centrales nucleares. Esta innovación transformó la detección de fallos en operaciones críticas al permitir la recopilación de datos del motor en tiempo real.
Sobre esta base, la ESA evolucionó para incluir la supervisión de la tensión y la potencia, ampliando sus capacidades a bombas, compresores y otros equipos rotativos en la década de 1990. Este enfoque no intrusivo se convirtió en esencial para minimizar los tiempos de inactividad y detectar problemas como el desgaste de los rodamientos y los desequilibrios del rotor.
En la década de 2010, la integración de datos en tiempo real y análisis avanzados impulsó la ESA hacia el mantenimiento predictivo, ayudando a los operadores a reducir costes y mejorar la eficiencia. En la actualidad, gracias a la IIoT y la IA, la ESA garantiza la fiabilidad al tiempo que impulsa la eficiencia energética y la sostenibilidad en todos los sectores.
Cómo funciona el SEC
El proceso de ESA consta de dos etapas principales: la captura y el análisis de datos. Ambas son esenciales para identificar fallos y mejorar la fiabilidad de la maquinaria.
Paso 1: Captura de datos
El primer paso del ESA consiste en instalar sensores permanentes en el armario de control del motor, donde pueden captar continuamente datos eléctricos de alta frecuencia de la máquina. Los sensores de ESA son diferentes de los utilizados en otros sistemas de control de estado, como el análisis de vibraciones, que requieren la colocación de sensores en la propia máquina. Con ESA, los sensores supervisan la corriente y la tensión de la máquina a distancia, sin necesidad de acceso físico directo.
Esto ofrece varias ventajas:
- Seguridad: Los sensores están protegidos de entornos adversos, como altas temperaturas o zonas peligrosas.
- Facilidad de instalación: Dado que los sensores se colocan en el armario de control del motor, están protegidos de riesgos operativos como el calor, las vibraciones o la exposición a líquidos.
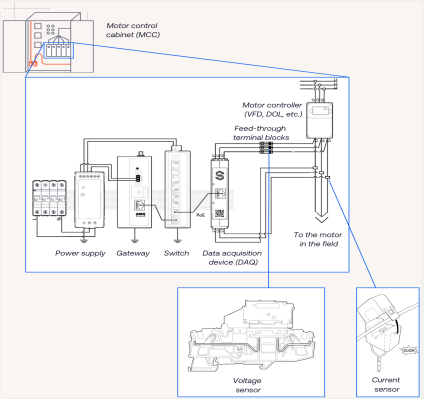
Paso 2: Análisis de datos
Una vez capturados los datos eléctricos, ESA utiliza diversos algoritmos para analizarlos. El algoritmo más fundamental de ESA es la transformada rápida de Fourier (FFT), que convierte los datos del dominio temporal al dominio de la frecuencia. Este análisis revela la firma de frecuencia de la máquina, un mapa detallado de su estado operativo.
Además de la FFT, la ESA utiliza otros métodos:
- Análisis espectral: Ayuda a determinar la intensidad de las distintas frecuencias de la señal eléctrica.
- Análisis de potencia: Identifica problemas como el desequilibrio de la tensión y la distorsión armónica, que pueden afectar al rendimiento de la máquina.
- Análisis lateral y de torsión: Proporciona información sobre los movimientos de rotación y vaivén de la máquina, lo que ofrece una imagen completa de su estado mecánico.
A través de este análisis continuo de datos, ESA puede identificar cambios en la firma eléctrica de la máquina que indican fallos en desarrollo. La recopilación de datos no intrusiva y el análisis exhaustivo del ESA lo convierten en una herramienta versátil y fiable para la supervisión de estado.
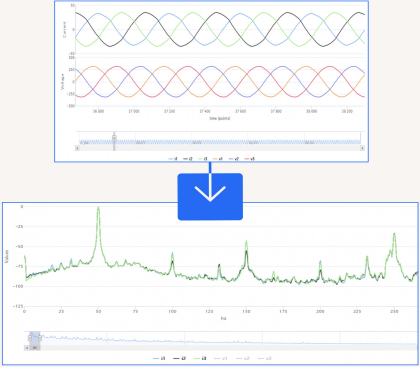
Tipos de fallos detectados por la ESA
La ESA es un método muy eficaz para descubrir fallos en los equipos mediante el análisis de cambios sutiles en la corriente y la tensión. Es excelente para detectar problemas mecánicos y eléctricos en una fase temprana, lo que permite realizar un mantenimiento específico antes de que los problemas se agraven. Al detectar estos fallos, la ESA ayuda a minimizar los tiempos de inactividad imprevistos y a prolongar la vida útil de los equipos.
Detección de fallos mecánicos con ESA
La ESA es excepcional a la hora de identificar fallos mecánicos en las máquinas. Los problemas mecánicos, como el desgaste de los rodamientos, los acoplamientos desalineados o la cavitación de la bomba, provocan cambios sutiles en el funcionamiento del motor, que afectan al campo magnético y, a su vez, a la firma eléctrica de la máquina. La ESA puede detectar estos cambios con antelación identificando huellas de frecuencia específicas de determinados fallos mecánicos.
Por ejemplo, cuando un rodamiento empieza a desgastarse, el ESA detectará un aumento de energía en frecuencias asociadas a las características físicas del rodamiento. Estas incluyen:
- Frecuencia fundamental del tren (jaula) - refleja el movimiento de la jaula que guía los elementos rodantes;
- Frecuencia de paso de bolas - indica posibles problemas con la pista interior del rodamiento;
- Frecuencia de paso de bolas - utilizado para detectar defectos en la pista exterior;
- Frecuencia de giro de la pelota - puede identificar defectos en los propios elementos rodantes.
Mediante el control de estas frecuencias, la ESA puede detectar la aparición de fallos mecánicos en el tren motriz, lo que permite repararlos a tiempo.
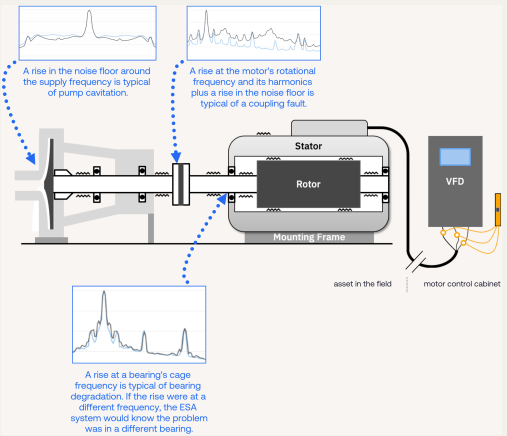
Detección de averías eléctricas con ESA
La ESA es especialmente eficaz en la detección de fallos eléctricos, que representan alrededor del 30% de las averías de motores en aplicaciones industriales. Los problemas eléctricos pueden repercutir directamente en el campo magnético de la máquina y, mediante el análisis de la corriente y la tensión, ESA permite detectar estos problemas en una fase temprana.
Algunos fallos eléctricos comunes que ESA puede identificar incluyen:
- Rotura de las barras del rotor: Estos provocan desequilibrios en el campo magnético del motor, y el ESA detecta las irregularidades en la firma eléctrica.
- Fallos del estátor: El ESA puede detectar problemas de aislamiento de los bobinados o cortocircuitos en el estátor antes de que se agraven.
- Corrientes de rodamiento: En determinados casos, las corrientes parásitas en los rodamientos pueden provocar un sobrecalentamiento y un desgaste prematuro. ESA puede detectar señales de estas corrientes a tiempo, ayudando a reducir el riesgo de daños mayores.
Como el ESA mide directamente la firma eléctrica de la máquina, puede detectar estos fallos antes que otros sistemas de control de estado que se centran en datos de vibración o temperatura.

Ventajas de la ESA: control del rendimiento y la energía en tiempo real
ESA es más que un sistema de detección de fallos: es una herramienta diseñada para mejorar el rendimiento de las máquinas y la eficiencia energética. Al proporcionar datos eléctricos en tiempo real, le ayuda a mantener la fiabilidad de sus operaciones y a identificar formas de reducir los costes energéticos.
Información en tiempo real para los retos cotidianos
ESA proporciona información sobre el rendimiento de sus máquinas, como vibraciones inusuales del motor que indican el desgaste de los rodamientos o picos de energía que apuntan a ineficiencias. Esta información le ayuda a planificar el mantenimiento, sustituir piezas antes de que se averíen y ajustar la configuración para mejorar la eficiencia. También le ayudan a tomar decisiones como actualizar los equipos o dar prioridad a las reparaciones de la maquinaria crítica.
Formas prácticas en que la AEE aporta valor añadido:
- Control de la eficacia de las bombas
Realiza un seguimiento del rendimiento de la bomba, aborda problemas como la cavitación y prolonga la vida útil de componentes clave como los cojinetes. - Control de la calidad de la energía
Detecta a tiempo problemas como desequilibrios de tensión o distorsión armónica, evitando problemas de rendimiento y pérdidas innecesarias de energía. - Seguimiento del consumo de energía
Analiza las tendencias a largo plazo en el uso de la energía para descubrir oportunidades de mejora de la eficiencia y ahorro de costes.
Una herramienta para simplificar la optimización
Gracias a la supervisión en tiempo real y a la información procesable, ESA es una solución práctica para mantener la fiabilidad y mejorar la eficiencia. Tanto si se trata de reducir el consumo de energía como de mejorar el rendimiento de la maquinaria, le ayuda a abordar las operaciones con confianza.
Principales industrias beneficiarias de la AEE
El análisis de firmas eléctricas ha demostrado ser indispensable en sectores en los que la fiabilidad y la eficiencia repercuten directamente en la rentabilidad y la seguridad. Al detectar fallos en una fase temprana y ofrecer información práctica, el ESA ayuda a las empresas a evitar costosas averías y mantener la excelencia operativa. He aquí ejemplos concretos de cómo ESA aporta valor en distintos sectores:
1. Fabricación
En entornos de producción de alta velocidad, incluso un fallo menor puede interrumpir las operaciones. ESA supervisa continuamente los motores y las cintas transportadoras para detectar problemas, como desequilibrios del rotor o desgaste de los rodamientos, habituales en las líneas de envasado o los sistemas de montaje. Al abordar estos problemas a tiempo, los fabricantes pueden evitar costosos retrasos en la producción y prolongar la vida útil de los equipos.
2. Energía y servicios públicos
Las centrales eléctricas utilizan la ESA para que los generadores, transformadores y sistemas de energía funcionen de forma óptima. Por ejemplo, puede detectar precozmente fallos en el aislamiento del bobinado del estator, evitando averías graves y protegiendo el suministro de energía. También ayuda a mantener una tensión equilibrada en todos los sistemas, mejorando la eficiencia y garantizando un rendimiento fiable.
3. 3. Petróleo y gas
En entornos remotos o peligrosos, como las plataformas marinas, la ESA resulta muy útil para supervisar bombas y compresores. Al detectar a tiempo la cavitación o las corrientes parásitas en los cojinetes, la ESA reduce el tiempo de inactividad y minimiza el riesgo de incidentes de seguridad. Su capacidad para funcionar en condiciones adversas lo convierte en una solución fiable para mantener el tiempo de actividad en este sector.
4. Transporte
Las redes ferroviarias y los sistemas de tránsito dependen de la ESA para mantener los motores eléctricos en condiciones óptimas. Por ejemplo, puede detectar el sobrecalentamiento o la desalineación de los motores que accionan los vagones, garantizando la seguridad de los pasajeros y evitando costosas interrupciones del servicio. La naturaleza no intrusiva de ESA es especialmente valiosa en estos sistemas de alta demanda.
5. 5. Tratamiento del agua
En instalaciones de agua y aguas residuales, la ESA supervisa bombas y motores para garantizar un funcionamiento ininterrumpido. Destaca en la detección de ineficiencias de flujo o cavitación que podrían comprometer el procesamiento del agua. Al mantener los sistemas en funcionamiento de forma eficiente, ESA contribuye a la prestación de un servicio constante en servicios públicos críticos.
6. Energía renovable
La ESA es un factor clave para la fiabilidad de los sistemas de energías renovables. Por ejemplo, en las turbinas eólicas, la ESA puede detectar el desgaste de la multiplicadora o fallos en el generador antes de que afecten a la producción de energía. Sus conocimientos ayudan a los operadores a reducir los costes de reparación y optimizar la producción de energía, en consonancia con los objetivos de sostenibilidad del sector.
7. Centros de datos
Dado que el tiempo de actividad no es negociable, los centros de datos utilizan ESA para supervisar las unidades de distribución de energía, los sistemas de refrigeración y los generadores de reserva. Identifica problemas como desequilibrios de tensión o sobrecalentamiento que podrían poner en peligro las operaciones. Al garantizar la fiabilidad de los equipos, ESA contribuye al funcionamiento continuo de estas instalaciones críticas.
Retos de la aplicación del SEC
La implantación de la ESA presenta varios retos que las organizaciones deben afrontar para aprovechar todo su potencial.
Conocimientos especializados es esencial para desplegar e interpretar eficazmente la ESA. Sin la formación adecuada, los equipos pueden tener dificultades para utilizar sus funciones avanzadas de detección de fallos.
Costes iniciales de sensores, hardware e integración también puede ser un obstáculo, especialmente para las empresas más pequeñas, aunque estas inversiones a menudo se amortizan gracias a la reducción del tiempo de inactividad y el ahorro en mantenimiento.
Gestión de grandes volúmenes de datos de alta frecuencia requiere herramientas eficaces para no perder información crítica.
Integración con los equipos existentes es otro reto, sobre todo en instalaciones con maquinaria antigua o variada, que puede requerir recursos adicionales para garantizar la compatibilidad.
Resistencia a adoptar nuevas tecnologías también es habitual, ya que los equipos pueden ceñirse a métodos conocidos y subestimar las ventajas de la AEE para mejorar la fiabilidad y la eficiencia energética.
Cómo empezar con la ESA
Emprender el viaje con el análisis de firmas eléctricas no tiene por qué ser desalentador. Si lo divide en pasos claros y manejables, podrá establecer un sistema eficaz que se adapte a su equipo y a sus necesidades operativas.
1. Defina sus objetivos de supervisión
¿Qué quiere conseguir? Tanto si se trata de detectar problemas en la barra del rotor en motores de inducción como de supervisar el desgaste del conmutador en motores de CC, unos objetivos claros guiarán su configuración. Tenga en cuenta factores como el entorno del equipo y el historial de mantenimiento para priorizar los aspectos en los que la ESA puede aportar más valor.
2. Trace su plan de ejecución
Planifique cómo encajará la ESA en sus operaciones actuales. Decida la ubicación de los sensores, la recogida de datos y los procesos de análisis. En el caso de activos críticos o de alta tensión, incluya precauciones de seguridad y redundancias adicionales. Un plan detallado garantiza una implantación sin problemas y maximiza los resultados.
3. Elegir al proveedor de sistemas de AEE adecuado
Elegir al proveedor de sistemas ESA adecuado puede facilitar mucho la implantación. Un proveedor fiable tendrá la experiencia necesaria para guiarle en cada paso, desde la instalación de los sensores hasta la integración del sistema. Busque un proveedor con experiencia en el sector, sólidos servicios de asistencia y soluciones escalables que se adapten a sus necesidades. Con el socio adecuado, disfrutará de una instalación perfecta con las mínimas interrupciones.
4. Garantizar una integración perfecta
Su sistema de ESA debe encajar sin esfuerzo en su infraestructura existente. Si utiliza plataformas IIoT, la integración puede ser sencilla. En el caso de equipos más antiguos, el proveedor adecuado puede ayudar a salvar las diferencias de compatibilidad, garantizando que su sistema funcione sin problemas.
5. Forme a su equipo
Dote a su equipo de los conocimientos que necesita para tener éxito. Ofrezca formación a medida: detección de fallos básicos para configuraciones más sencillas y diagnósticos avanzados para sistemas más complejos. Un equipo seguro de sí mismo es esencial para interpretar los datos y actuar con eficacia.
ESA frente a otras técnicas de Condition Monitoring
La ESA destaca en la detección de averías tanto eléctricas como mecánicas, lo que le permite obtener información muy valiosa, difícil de igualar por otros métodos. Una de sus ventajas más destacadas es su capacidad para supervisar activos de difícil acceso, como bombas sumergidas, motores encapsulados o equipos situados en zonas peligrosas o restringidas. Con sensores instalados de forma segura en el armario de control del motor, ESA elimina la necesidad de acceder directamente al equipo, lo que lo convierte en una solución práctica y eficaz para entornos difíciles.
A continuación, comparamos la ESA con el análisis de vibraciones y la termografía -otras dos técnicas muy utilizadas- para destacar los puntos fuertes y las limitaciones de cada una. Esta comparación puede ayudarle a determinar qué método se ajusta mejor a sus necesidades operativas.
Característica | Análisis de firmas eléctricas (ESA) | Análisis de vibraciones | Imagen térmica (infrarrojos) |
Método de control | No intrusivo, basado en datos eléctricos (corriente y tensión) | Intrusivo, basado en datos de vibraciones físicas | No intrusivo, basado en lecturas de la temperatura de la superficie |
Tipo de datos analizados | Señales de corriente y tensión | Señales de vibración | Firmas de calor infrarrojo |
Fallos detectados | Eléctricos (p. ej., barras del rotor) y mecánicos (p. ej., desgaste de los rodamientos) | Principalmente mecánicos (por ejemplo, desalineaciones, desgaste de rodamientos) | Sobrecalentamiento, averías de aislamiento, desequilibrios térmicos |
Colocación del sensor | Sensores en el armario de control del motor, sin contacto directo con el equipo | Sensores colocados directamente en los equipos | Se requiere línea de visión, sin contacto directo con el equipo |
Idoneidad para la supervisión a distancia | Muy adecuado, ideal para lugares inaccesibles o peligrosos | Limitado, requiere la colocación de sensores en el lugar | Limitado, requiere acceso visual directo a los componentes |
Momento de la detección | Detección precoz, a menudo antes de que se produzcan anomalías de vibración o temperatura | Intermedio, a menudo después de que se hayan desarrollado fallos | Intermedio, detecta fallos existentes pero no es predictivo |
Escalabilidad | Alto, fácilmente escalable a través de múltiples activos | Moderado, requiere sensores en cada activo | Las inspecciones manuales limitan la escalabilidad |
Integración con IIoT | Altamente compatible, se integra con plataformas IIoT para análisis avanzados | Moderadamente compatible, requiere configuración adicional para IIoT | Baja compatibilidad, suele ser una herramienta independiente |
Coste de aplicación | Moderado a alto (coste inicial pero ahorro a largo plazo) | Moderado (el coste del sensor depende del número de activos supervisados) | Bajo a moderado (las cámaras portátiles pueden ser rentables) |
¿Por qué elegir ESA en lugar de otras técnicas de Condition Monitoring?
La ESA ofrece una ventaja significativa para detectar fallos eléctricos, como barras de rotor rotas y problemas en el estátor, donde resulta más eficaz y económica que otras técnicas. Aunque los fallos en los rodamientos pueden detectarse más fácilmente mediante el análisis de vibraciones, la ESA también puede detectarlos, lo que la convierte en una solución versátil.
Además, el ESA también puede identificar fallos como desalineaciones mecánicas, problemas de entrehierro, irregularidades en la alimentación y problemas de aislamiento, lo que lo convierte en una herramienta completa para el diagnóstico de motores. Su facilidad de implementación, incluso en activos de difícil acceso como bombas sumergidas o equipos en zonas peligrosas, se suma a su practicidad. En combinación con su compatibilidad con los sistemas IIoT y su escalabilidad, la ESA es un excelente método de monitorización de estado independiente o complementario para una detección de fallos y un análisis de causa raíz más amplios.
Casos prácticos de la ESA y ejemplos reales
Desde la mejora de la fiabilidad de las bombas en las centrales eléctricas hasta la detección de fallos en los transformadores de los sistemas de energía eólica y el diagnóstico de problemas en las cajas de engranajes de los equipos industriales, la ESA ha demostrado su valor en diversas aplicaciones. Estos ejemplos reales muestran cómo la ESA permite un mantenimiento oportuno y optimiza el rendimiento de los equipos:
1. Mejora de la fiabilidad de las bombas en una central eléctrica
En una instalación de energía nuclear, se utilizó ESA para supervisar dos motores de 350 caballos de potencia que accionaban bombas verticales de agua de servicio. Los métodos de prueba tradicionales no detectaron los problemas de rendimiento subyacentes, pero ESA identificó rápidamente turbulencias en el sistema causadas por fallos mecánicos. La detección temprana permitió a la planta tomar medidas correctivas a tiempo, evitando paradas imprevistas y garantizando que las operaciones críticas continuaran sin problemas.
2. Identificación de los problemas de los transformadores en la energía eólica
En otro caso, la ESA se aplicó a un transformador de un sistema de energía eólica para descubrir anomalías de funcionamiento. El análisis reveló importantes desequilibrios eléctricos y conexiones sueltas que no eran visibles con las técnicas de control habituales. El tratamiento de estos fallos no sólo resolvió el problema inmediato, sino que también mejoró la fiabilidad a largo plazo del transformador.
3. Localización de averías en cajas de cambios de equipos industriales
En una aplicación industrial, se utilizó ESA para analizar un motor y su caja de engranajes acoplada. Los datos revelaron una señal inusual que indicaba holgura en el exterior del motor, lo que permitió localizar una caja de engranajes defectuosa. Esta información permitió a los equipos de mantenimiento actuar antes de que el problema se agravara, evitando costosas paradas imprevistas y prolongando la vida útil del equipo.
Tendencias futuras de la tecnología de la AEE
El futuro del Análisis de Firma Eléctrica (ESA) está siendo moldeado por una combinación de avances tecnológicos y la creciente demanda de fiabilidad, eficiencia y sostenibilidad en las operaciones industriales. El ESA está evolucionando de una herramienta tradicional de monitorización de estado a una solución predictiva que proporciona una detección de fallos más temprana y precisa.
Las innovaciones clave, como la IA y el aprendizaje automático, están impulsando la evolución de ESA de una herramienta reactiva a una solución de mantenimiento predictivo, proporcionando información procesable que mejora la toma de decisiones. Como complemento, la integración de ESA con plataformas del Internet Industrial de las Cosas (IIoT) y análisis basados en la nube permite una supervisión escalable y en tiempo real en múltiples instalaciones. Esto reduce la dependencia de los recursos in situ y permite dar respuestas más rápidas y eficaces a los posibles problemas.
Al mismo tiempo, la tecnología de sensores es cada vez más robusta y precisa, lo que garantiza un rendimiento fiable incluso en entornos difíciles o complejos. El procesamiento de datos centralizado y los algoritmos avanzados, como la transformada rápida de Fourier (FFT), mejoran aún más la precisión de la detección de fallos y agilizan el diagnóstico. Combinados con interfaces de usuario intuitivas, estos avances hacen que la ESA sea cada vez más práctica y accesible en todos los sectores.
Mediante la combinación de análisis predictivos, integración perfecta y diseño fácil de usar, ESA no sólo sigue el ritmo de los avances tecnológicos, sino que también da forma al futuro de la monitorización de estado y la protección de máquinas.
Sistema ESA "Samotics" (SAM4)
Sistema ESA "SamoticsSAM4, lleva la monitorización de estado al siguiente nivel combinando el aprendizaje automático avanzado con la recopilación de datos eléctricos de alta frecuencia. Instalado directamente en el armario de control del motor, proporciona información que le ayuda a mantener sus activos en funcionamiento de forma fiable, eficiente y sostenible.
Supervisión remota, incluso en entornos difíciles
Con sensores instalados de forma segura en el armario de control del motor, SAM4 captura datos de corriente y tensión las 24 horas del día, los 7 días de la semana, sin necesidad de acceder al propio equipo. Esto lo hace perfecto para ubicaciones de difícil acceso o peligrosas, como bombas sumergidas, motores encapsulados en maquinaria o zonas ATEX. Y lo que es mejor, la instalación es rápida y sencilla: suele llevar menos de 30 minutos por máquina.
Detección precoz y precisa de averías
SAM4 destaca en la detección de problemas eléctricos y mecánicos antes de que provoquen tiempos de inactividad. Desde daños en la barra del rotor hasta acoplamientos desalineados, SAM4 detecta más de 90% de averías, a menudo con hasta cinco meses de antelación. Al supervisar cómo afectan los problemas mecánicos a las señales eléctricas, SAM4 le proporciona la información que necesita para actuar a tiempo y evitar costosas averías.
Optimice el rendimiento y reduzca los costes energéticos
SAM4 no sólo detecta problemas, sino que también le ayuda a gestionar mejor su equipo. Sus herramientas avanzadas incluyen:
- Control de bombas para mantener las bombas en su punto de funcionamiento más eficiente, reduciendo el desgaste.
- Control de la energía para poner de manifiesto las ineficiencias e identificar los puntos en los que un rediseño o sustitución podría ahorrar dinero y energía.
- Control de la calidad de la energía para solucionar problemas de suministro como el desequilibrio de la tensión y la distorsión armónica.
Conclusión
ESA es una potente solución para mejorar la fiabilidad y la eficiencia operativa en diversos sectores. Gracias a la detección temprana de fallos, la mejora de la eficiencia energética y la información en tiempo real, ESA permite a las empresas optimizar sus estrategias de mantenimiento, reducir costes y aumentar la fiabilidad.
Tanto si se trata de evitar tiempos de inactividad imprevistos en la fabricación como de proteger infraestructuras críticas en la generación de energía o mantener el tiempo de actividad en entornos difíciles como plataformas petrolíferas e instalaciones de tratamiento de aguas, la ESA ofrece un valor cuantificable. Su capacidad para integrarse a la perfección con las plataformas IIoT y aprovechar los análisis basados en IA la sitúan como una solución preparada para el futuro en un mundo cada vez más centrado en la sostenibilidad y la eficiencia.
Para las empresas que buscan adelantarse a la evolución de la demanda y a las presiones competitivas, la ESA debe considerarse una inversión estratégica en fiabilidad, ahorro de costes y crecimiento sostenible.
Si está listo para descubrir cómo la ESA puede transformar sus operaciones, estaremos encantados de informarle sobre nuestra solución de ESA, SAM4.
Preguntas frecuentes sobre la ESA
¿Cómo mejora la AEE la eficiencia energética?
Mediante el seguimiento del consumo de energía y la identificación de ineficiencias como armónicos o desequilibrios de carga, ESA pone de relieve áreas de mejora que pueden reducir los costes energéticos.
¿Con qué frecuencia deben analizarse los datos del SEC?
La frecuencia de los análisis depende de la criticidad del equipo, pero se prefiere la supervisión en tiempo real para los activos de alto valor o críticos.
¿Funciona ESA con variadores de frecuencia (VFD)?
Sí, ESA puede supervisar motores controlados por variadores de frecuencia, pero el análisis puede requerir ajustes debido al ruido eléctrico generado por los variadores.
¿En cuánto tiempo puedo esperar resultados del uso de ESA?
Beneficios como la detección de fallos y la información energética pueden obtenerse inmediatamente, mientras que el ahorro a largo plazo aumenta con el tiempo a medida que se abordan las tendencias y la eficiencia.
¿Es la ESA escalable para grandes instalaciones?
Sí, los sistemas ESA pueden supervisar múltiples activos en una instalación de gran tamaño, con un software centralizado para analizar y mostrar los datos de rendimiento en tiempo real.
¿Puede utilizarse la ESA en instalaciones de vigilancia a distancia?
Sí, muchas soluciones de AEE ofrecen funciones de supervisión remota, lo que permite a los operadores hacer un seguimiento del rendimiento de los equipos y del uso de la energía desde cualquier lugar.
¿Qué se necesita para integrar la ESA en los sistemas existentes?
Los sistemas ESA suelen requerir acceso al cuadro eléctrico y pueden integrarse con plataformas existentes de supervisión de estado o gestión de activos mediante software o API.
¿Cuál es el ahorro monetario a largo plazo que puedo esperar del SEC?
Por ejemplo, una bomba de agua que funcione continuamente a 100 kW con un coste eléctrico de 0,10 euros por kWh consumiría unos 87.600 euros de energía al año. Si se utiliza la ESA para detectar a tiempo problemas como la cavitación, la eficiencia energética puede mejorar en aproximadamente 10%, lo que supone un ahorro anual de unos 8.760 euros. La mayoría de las industrias recuperan la inversión en 1-3 años, lo que convierte a la ESA en una opción inteligente para reducir costes y mejorar la eficiencia operativa.